Optimizing Production Efficiency with Flexible Metal Parts Feeding
Introduction: The Global Manufacturing Sector
The global manufacturing sector, undergoing radical transformations through digitization and automation, is the backbone of the world economy. It is continually seeking innovative solutions for enhancing efficiency and reducing costs. One such technology, gaining increasing relevance, is the use of flexible parts feeding in handling metal components.
The Evolving Landscape: Technological Innovations and Production Challenges
The manufacturing industry, characterized by high volumes and extensive variability in components, constantly faces challenges arising from shifting consumer demands, environmental considerations, and technological advancements. Effective management of these challenges necessitates the adoption of agile and sustainable practices.
Adapting to Industry 4.0: The Role of Flexible Parts Feeders in the Handling of Metal Components
With the advent of Industry 4.0, manufacturers are rapidly transitioning towards automated, intelligent production lines. At the heart of this transformation is flexible parts feeding, a method that provides enhanced adaptability in handling an array of metal components.
Metal Parts Feeder: The Case of FlexiBowl
FlexiBowl, a leading example of a metal parts feeder, offers several key advantages:
- Versatility: FlexiBowl can handle a variety of part shapes and sizes, thereby eliminating the need for multiple feeders.
- Increased Efficiency: The technology reduces downtime due to feeder changeovers, enhancing production speed.
- Adaptability: It enables swift and smooth transitions between different parts, thereby improving the overall workflow.
A flexible feeder like FlexiBowl can be utilized in various production processes, especially when dealing with components ranging from 1 to 300 mm. In the manufacturing sector, a flexible parts feeder can bring substantial benefits to several production processes, including assembly, quality control and inspection, precision machining, packaging, grinding, milling and turning, injection molding, stamping, punching, trimming, forging, compression molding, and welding.
Cylindrical
Complex
Flat
Metal Parts Feeding: Broad Spectrum of Applications
Metal parts feeding systems are employed across a wide variety of industries, including automotive production, aeronautical industry, electronics production, machinery manufacturing, jewelry production, medical equipment production, and the energy industry.
Advantages of Using a Flexible Feeder like FlexiBowl
Apart from the aforementioned versatility, efficiency, and adaptability, a flexible feeder like FlexiBowl offers several other benefits:
-
- Reduced Noise: As an alternative to vibratory feeders, flexible feeders operate with less noise, thereby enhancing the working environment and mitigating the need for noise protection.
- Prevention of Jamming: Flexible feeders, being designed to accommodate components of complex or irregular shapes, successfully reduce the risk of jams and production interruptions.
- Multi-Component Handling: Due to their versatility, flexible feeders can manage various types of components simultaneously, hence eliminating the need for multiple feeders and conserving both space and costs.
- High Adaptability: A flexible feeder easily adapts to different sizes and shapes of parts, doing away with the need for costly reconfigurations or equipment replacements.
- Energy Efficiency: As an alternative to vibratory feeders, flexible feeders generally consume less energy, thereby contributing to lower operational costs.
- Time Saving: Requiring less time for setup and adjustment to handle parts, flexible feeders enhance production efficiency.
- Gentle Handling: Contrary to vibratory systems, flexible feeders handle parts gently, reducing the risk of damage to delicate or finely worked components.
- Better Component Separation: Flexible feeders are designed to accurately distinguish components with similar properties, thus reducing feeding and assembly errors.
Types of Metallic Parts a Flexible Feeder Can Handle
Flexible feeders can handle a variety of metal parts, including screws, bolts, washers, retaining rings, nails, pins, brackets, nuts, bars, rivets, and more.
Embracing the Future of Manufacturing
The future success of the manufacturing industry depends on its ability to innovate, adapt, and respond to an ever-changing production landscape. In this context, flexible parts feeding devices like FlexiBowl are poised to play an essential role, offering increased productivity, reduced costs, and improved overall efficiency.
Videos

30 x 20 mm

20 x 10 mm

40x 10 mm

30 x 5 mm
What advantages does the FlexiBowl solution bring in for machine tending applications?
FlexiBowl is a standardized vision and robotic based equipment that be used for feeding parts in the metalworking industry. Parts ranging 1-250 mm and 1-250 mm no matter their geometry and material can be handled. The high payload, up to 7 kg, and the robust and reliable mechanical design make the FlexiBowl a perfect match for robotic applications in the metalworking industry.
How does a FlexiBowl cope with dirty and oily parts?
An oil channel can applied optionally to dry the Flexibowl up of working fluids left on the parts during upstream processes. A special configuration with remote control box secures the inside electronics from being affected by metal powder and chips resulting from machining manufacturing processes. The rotary discs can be switched over rapidly thanks to the quick changeover mechanism that minimizes downtime during maintenance operations.
Main end users

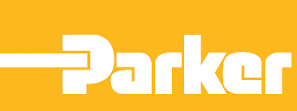
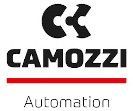
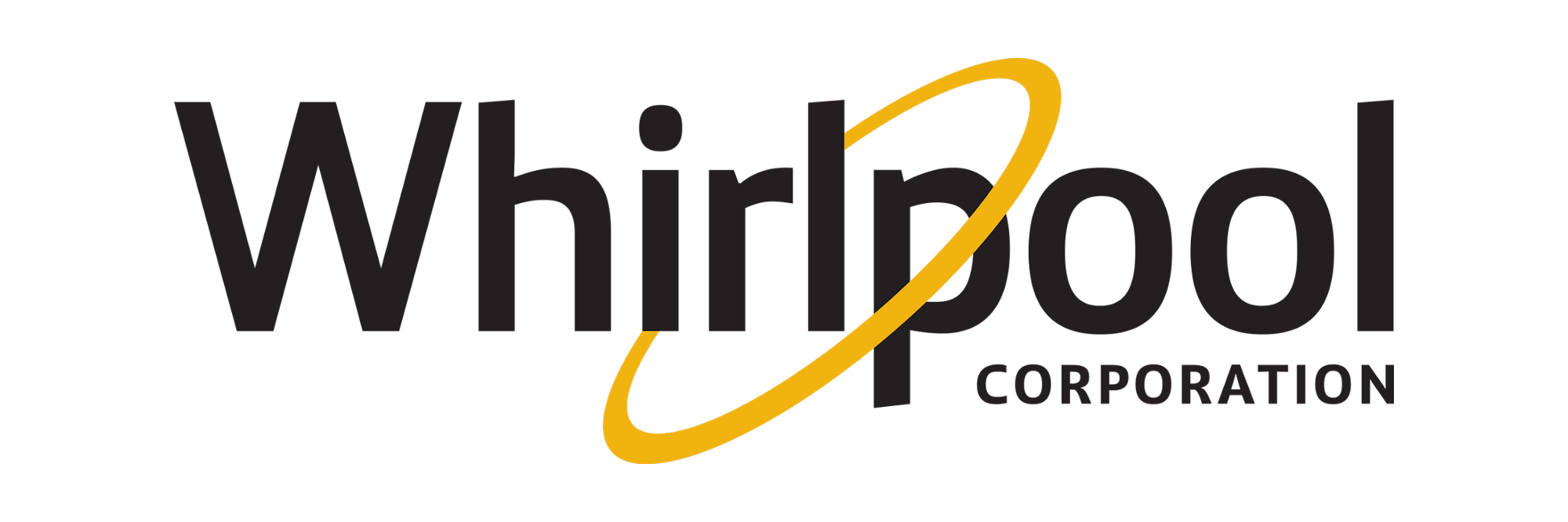
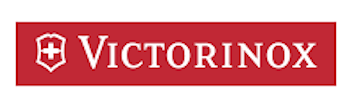
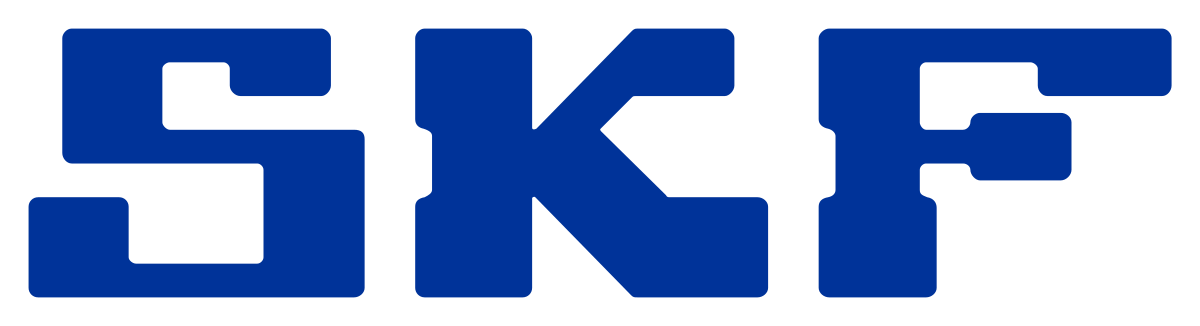
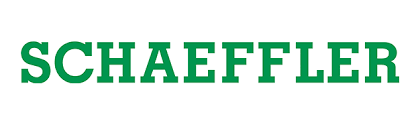
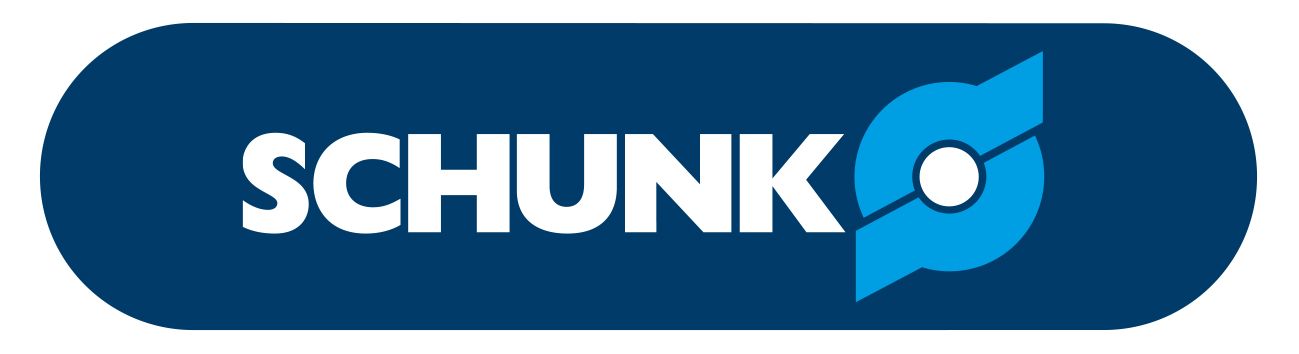
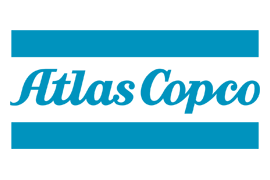
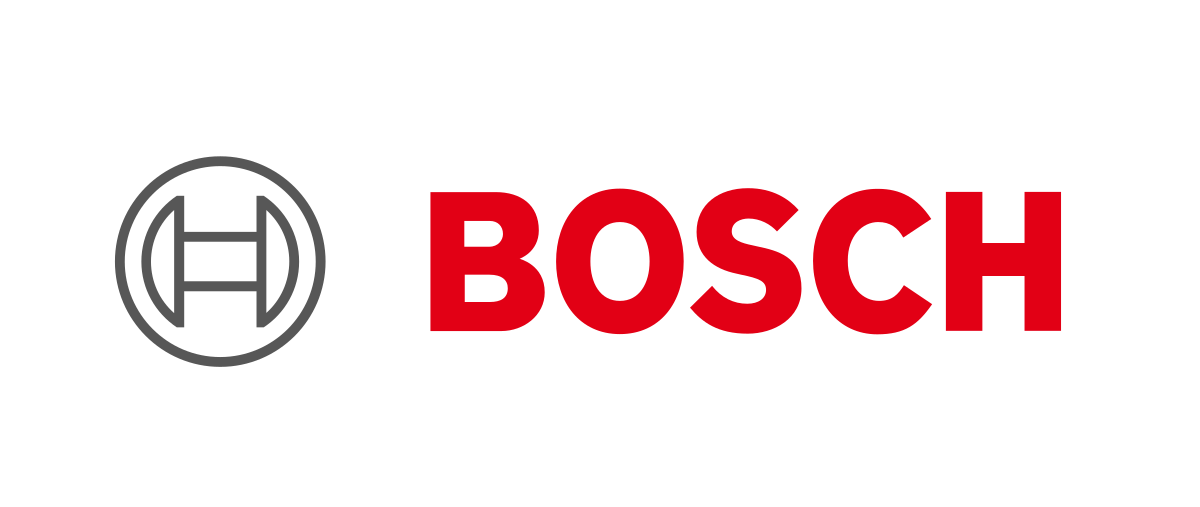