Introduction: The Crucial Role of Plastic Parts Feeders in Automation
Explore the critical importance of plastic parts feeders in the landscape of factory automation. In a world where manufacturing sectors are continually confronted with assembly operation challenges, proficient management of plastic components becomes paramount. Discover how flexible parts feeders, epitomized by FlexiBowl, are transforming sectors such as medical device manufacturing, food and beverage production, cosmetics, toy production, and electronics.
How Plastic Parts Feeders Like FlexiBowl Enhance Production
FlexiBowl brings a multitude of advantages over traditional vibratory feeding systems:
- Diminished Sound Emission: By operating more quietly, it cultivates an improved workplace, reducing the necessity for soundproofing measures.
- Blockage Avoidance: Its design optimizes the handling of intricate or irregularly formed parts, significantly lowering the chances of blockages and disruption in the manufacturing process.
- Handling of Multiple Elements: FlexiBowl's adaptability enables concurrent management of diverse components, eliminating the requirement for numerous feeders, preserving space, and decreasing expenses.
- Great Versatility: FlexiBowl comfortably accommodates various part sizes and forms, thereby bypassing expensive equipment alterations or replacements.
- Energy Conservation: By using less energy than conventional vibratory feeders, it aids in reducing operational expenses.
- Efficient Time Utilization: It necessitates less time for setup and adjustments, boosting production efficacy.
- Tender Handling: FlexiBowl processes parts delicately, lessening the potential for harm to fragile or intricately crafted components.
- Enhanced Part Singulation: It's engineered to precisely identify and separate components with analogous features, lessening feeding and assembly inaccuracies.
Types of Plastic Parts a Flexible feeding system Can Handle
FlexiBowl effectively handles a broad range of plastic parts, from 1 to 300 mm, including:
- Various sizes of plastic bottles, containers, and lids used across numerous applications.
- Plastic components of different sizes and shapes used in the healthcare and cosmetic industries.
- Plastic tubes of various dimensions utilized in many industrial applications.
- Plastic caps for bottles of cosmetic or medical products.
- Plastic bands of different sizes used in various applications.
- Various-sized makeup applicators, pads, and other components used in the cosmetic industry.
- Soft plastic components used in toy manufacturing.
- Plastic seals, springs, clips, taps, clamps of varying sizes used in numerous industrial and applications.
Cylindrical Plastic Parts
Complex Plastic Components
Flat
Vision Systems in Flexible Parts Assembly
The success of a flexible feeding system heavily depends on its inherent flexibility and integration with diverse robots and vision systems. Integration with robots allows efficient handling of infeed components, pallets, fixtures, tools, and the outfeed of finished parts. The incorporation of a vision system significantly aids these processes by offering quality and dimensional checks and guidance for the robots.
Factors Influencing Vision System Performance
To implement a successful vision system, various factors need consideration, including:
- The characteristics of the parts (size, shape, color, and texture)
- Camera specifications (sensor resolution, quality of lenses)
- Quality of system calibration
- Working environment (lighting conditions and position)
Vision algorithms are typically sensitive to these environmental conditions, and efficient processing time is crucial when integrating a vision system for robot guidance in assembly processes.
Advantages of FlexiBowl® for Plastic Parts Assembly
FlexiBowl® is a flexible feeding device that integrates seamlessly with every robot and vision system brand. It can handle an entire range of parts within 1-250 mm and 1-250 g, eliminating the need for multiple dedicated vibratory bowl feeders. Its quick changeover mechanism ensures minimal downtime during maintenance operations. The absence of dedicated tooling and user-friendly software enables swift and multiple product changeovers within the same work shift.
The Future of Plastic Parts Feeders
In an intensely demanding and competitive plastics industry market, achieving low costs, high quality, and prompt delivery times is paramount for success. This is where robotics and flexible automation come into play as they help businesses meet market demand, maintain margins, and re-shore production. Deploying a robot on the manufacturing floor not only paves the way for more stimulating and intelligent job positions but also propels businesses into the Industry 4.0 era. Here, smart production sites comprise connected machines that communicate via the Internet of Things and individuals that collect information to make decisions. Thus, the effective use of robotics and flexible feeding systems like FlexiBowl can lead to increased productivity, decreased parts waste, improved production rates, and cost-effectiveness, all of which contribute to a more competitive and efficient plastic parts manufacturing industry.
Videos
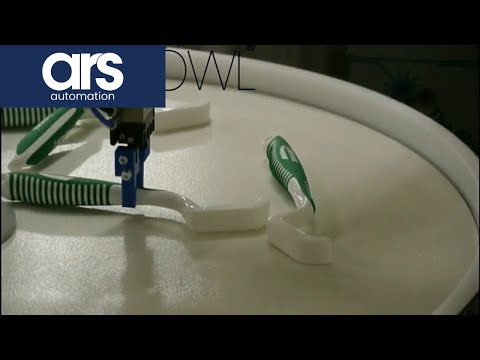
250 x 25 mm

30 x 15 mm

25 x 10 mm

35 x 20 mm
Plastic parts feeders: what advantages does
the FlexiBowl solution bring in for machine tending applications?
FlexiBowl is a standardized vision and robotic based equipment that be used for feeding parts in the plastic industry. Parts ranging 1-250 mm and 1-250 mm no matter their geometry and material can be handled.
Its lack of dedicated tooling and its easy to use and intuitive programming software allows quick and multiple product changeovers inside the same work shift.
The high payload, up to 7 kg, and the robust and reliable mechanical design make the FlexiBowl a perfect match for robotic applications in the plastic industry.
Main end users
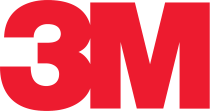
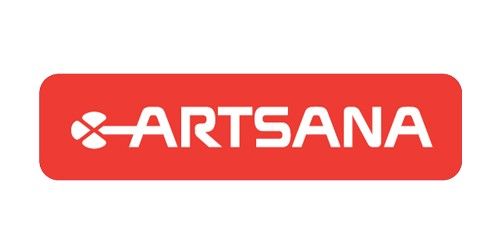
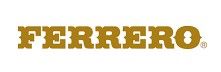