Optimizing Production Efficiency with Flexible Non-Rigid Parts Feeding
Introduction: Non-Rigid Materials Parts Feeding
Discover the critical role of Non-Rigid Materials Parts Feeding in factory automation. As the global manufacturing sector faces challenges in assembly operations, the efficient handling of non-rigid components becomes essential. Learn how flexible parts feeding, exemplified by FlexiBowl, revolutionizes industries like medical device production, food and beverage production, cosmetics, toy manufacturing, and electronics.
Advantages of Flexible Feeders like FlexiBowl.
FlexiBowl offers a multitude of advantages over traditional vibratory feeding systems:
- Reduced Noise: Operating with less noise creates a better working environment and reduces the need for noise protection.
- Prevention of Blockages: Its design efficiently handles complex or irregularly shaped components, significantly reducing the risk of blockages and production interruptions.
- Multi-Component Handling: The versatility of FlexiBowl allows simultaneous handling of different component types, eliminating the need for multiple feeders, saving space, and reducing costs.
- High Adaptability: FlexiBowl easily adapts to various part sizes and shapes, avoiding expensive reconfigurations or equipment replacements.
- Energy Efficiency: It consumes less energy than traditional vibratory feeders, contributing to lower operational costs.
- Time-Saving: Requiring less setup and adjustment time, FlexiBowl enhances production efficiency.
- Gentle Handling: FlexiBowl handles parts gently, reducing the risk of damage to delicate or intricately worked components.
- Better Component Separation: Designed to accurately distinguish components with similar properties, it reduces feeding and assembly errors.
Types of non-rigid materials that a flexible feeder can handle:
FlexiBowl effectively handles a wide range of non-rigid materials, from 1 to 300 mm, including:
- Various sizes of rubber or silicone O-rings are used for sealing connections across numerous applications.
- Sponges of different sizes are used in the healthcare and cosmetic industries.
- Silicone tubes of various dimensions are utilized in many industrial applications.
- Silicone caps for bottles of cosmetic or medical products.
- Elastic bands of different sizes are used in various applications.
- Different-sized makeup applicators, pads, and other components are used in the cosmetic industry.
- Soft plastic components used in toy manufacturing.
- Seals and springs of varying sizes are used in many industrial and medical applications.
Cylindrical
Complex
Flat
Videos
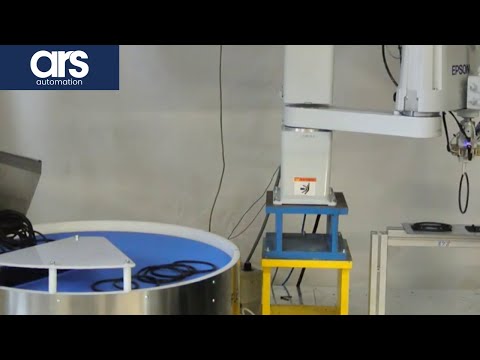
100 x 3 mm
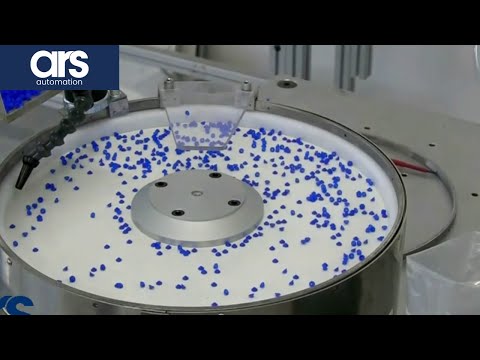
1 x 1 mm

30 x 30 mm
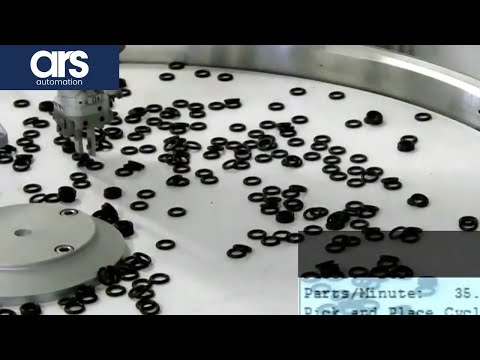
10 x 4 mm
The Importance of Vision Systems in Non-Rigid Materials Parts Feeding.
The success of a flexible feeding system heavily relies on its inherent flexibility and integration with various robots and vision systems. Integration with robots enables efficient handling of input components, pallets, fixtures, tools, and the outfeed of finished parts. The addition of a vision system greatly assists these processes by providing quality and dimensional checks, as well as instructions for the robots.
The factors influencing vision system performance:
Implementing a successful vision system requires considering various factors, including:
- The characteristics of the parts (size, shape, color, and texture)
- Camera specifications (sensor resolution, quality of lenses)
- Quality of system calibration
- Working environment (lighting conditions and position)
Vision algorithms are typically sensitive to these environmental conditions, and efficient processing time is crucial when integrating a vision system for robot guidance in assembly processes.
Advantages of FlexiBowl® for flexible parts assembly.
FlexiBowl® is a flexible feeding device that seamlessly integrates with every robot and vision system brand. It can handle entire families of parts within 1-250 mm and 1-250 g, replacing the need for multiple dedicated vibratory bowl feeders. With its quick changeover mechanism, maintenance operations cause minimal downtime. The lack of dedicated tooling and user-friendly software enable quick and multiple product changeovers within the same work shift.
Main End Users
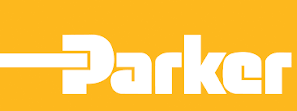
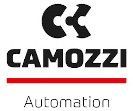
