Challenges and Opportunities: Flexible Parts Feeding in the Cosmetics & Personal Care Industry
The Cosmetics & Personal Care industry is a highly competitive market. Companies are continuously striving to meet the discerning needs of consumers, focusing on product quality and sustainability. Adapting to evolving market trends and maintaining an openness to change is crucial. Among the innovations shaping the industry is the flexible parts feeding system for cosmetic and personal care parts.
Technological Advances and Production Challenges in the Dynamic Cosmetics Landscape
Continuous innovation, including the use of a Cosmetics & Personal parts feeder , is key to securing a leading position in the Cosmetics & Personal Care industry. Efficient and flexible production lines, especially those equipped with quick setup times, are essential to stay competitive in today's dynamic market.
The Advent of Industry 4.0: The Shift Towards Flexible Components Feeding
With the rise of Industry 4.0 technologies, cosmetic and personal care manufacturers are under pressure to adapt their production lines. The flexible part feeder, capable of handling a wide range of components, is at the core of this transformation.
Cylindrical
Flat
FlexiBowl®, The Universal Cosmetic & Personal Care Parts Feeder
FlexiBowl®, as a leading example of a Cosmetic & Personal Care parts feeder, offers numerous advantages:
- Versatility
FlexiBowl® can handle a variety of product shapes, sizes, and materials, including delicate items like perfume bottles, lipstick caps, mascara wands, nail polish wands, and jar lids, eliminating the need for multiple vibratory feeders. - Efficiency
By reducing downtime due to feeder changeovers, FlexiBowl® significantly increases production speed. - Adaptability
FlexiBowl® allows for rapid and smooth transitions between different parts, thus enhancing the overall workflow.
Implementing FlexiBowl®: How the Cosmetic & Personal Care Parts Feeder Transforms Production Processes
A flexible feeder like FlexiBowl® can be implemented across various production processes, especially when dealing with components of different sizes.
- Assembly and pre-assembly
- Filling and capping
- painting
- quality inspection
- packaging
- printing and marking
FlexiBowl® can be used to feed parts of varying sizes to the pre-assembly process, adapting its operation based on the size of the component being handled.
By reducing the risk of product damage and costs associated with rejected components, FlexiBowl® upholds high-quality standards.Suitable for variable batch production, FlexiBowl ensures high cycle times, making it an efficient solution for Cosmetic & Personal Care parts feeding.
The FlexiBowl® Advantage: A Game Changer for the Cosmetics & Personal Care Industry
FlexiBowl® offers numerous benefits as a leading solution in flexible parts feeding technology:
- Ease of Integration
FlexiBowl® is designed to seamlessly fit into any production project, simplifying its integration into existing systems. - Production Flexibility
The system can easily adapt to any changes in production, demonstrating its flexibility and adaptability. - Delicate Handling
FlexiBowl®carefully handles small and delicate products, reducing the risk of unwanted damage.
FlexiBowl®'s Capability: Types of Components in Cosmetics & Personal Care It Can Handle
- Closures
FlexiBowl® is capable of handling various closures such as screw caps, flip-top caps, pump and press caps, pipettes, droppers, diffusers, roll-ons, seals, disks, and inserts. - Containers
This includes bottles, jars, and vials. - Applicators
FlexiBowl® can deal with brushes with spiral, cone, flat bristle, and crimped bristle shapes, among others.
Looking Forward: The Role of Flexible Parts Feeders in the Future of Cosmetics & Personal Care Production
The future success of the Cosmetics & Personal Care industry hinges on its ability to adapt, innovate, and respond to an evolving production landscape. Flexible parts feeding devices like FlexiBowl® are set to play a critical role in this transformation.
Videos
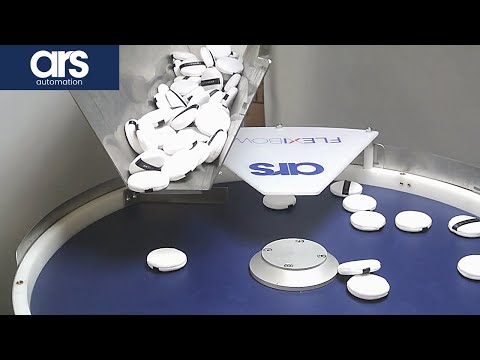
50 x 10 mm

20 x 15 mm
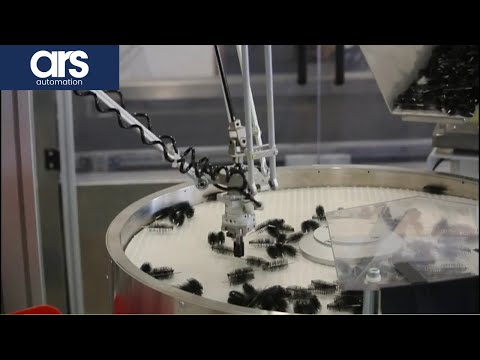
30 x 5 mm

120 x 10 mm
Main end users
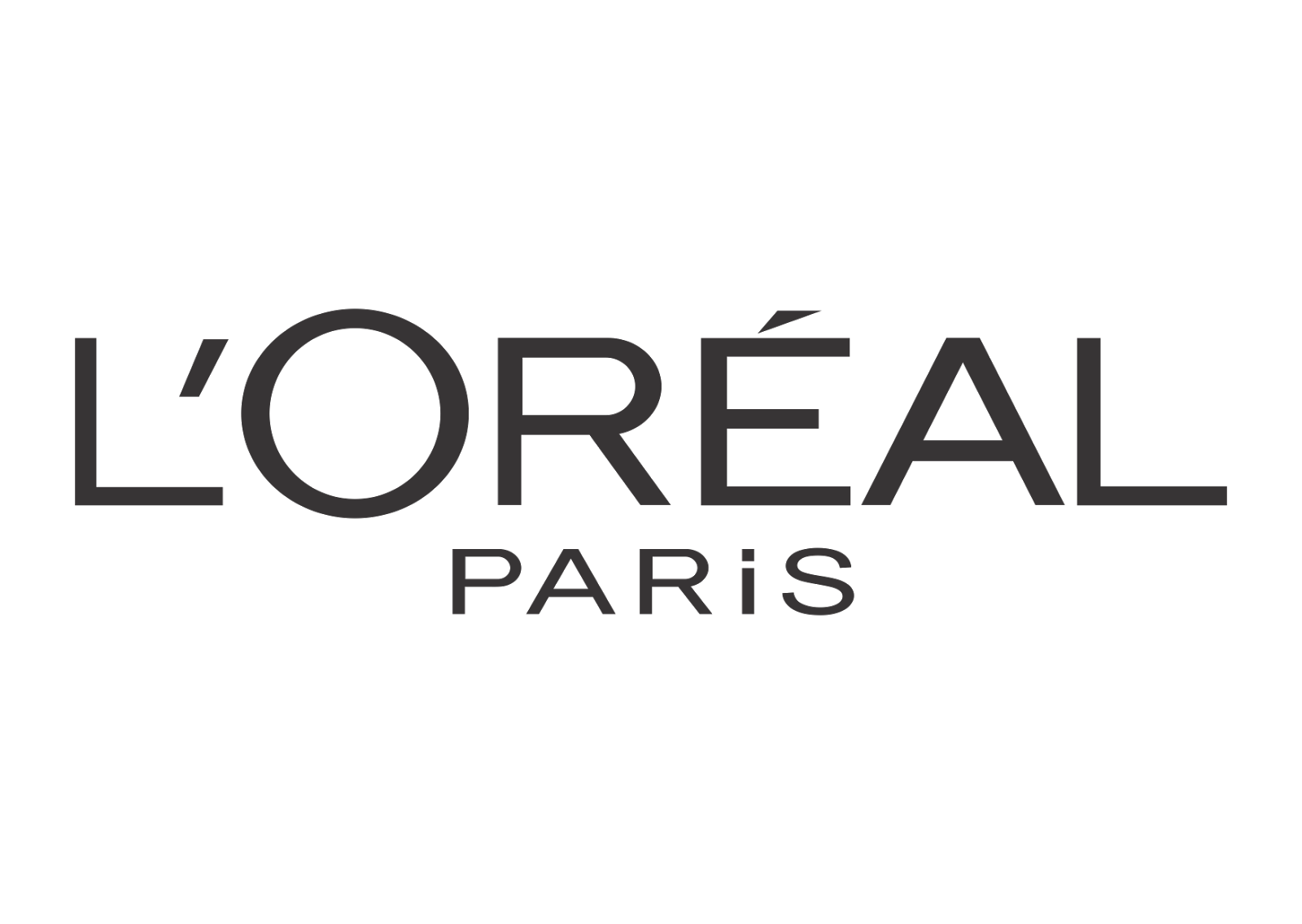
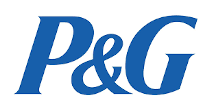
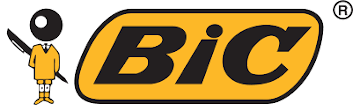
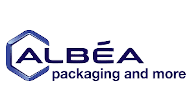
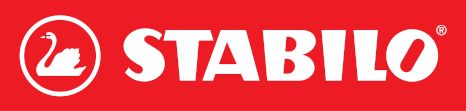
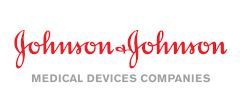
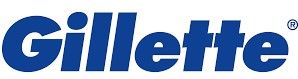
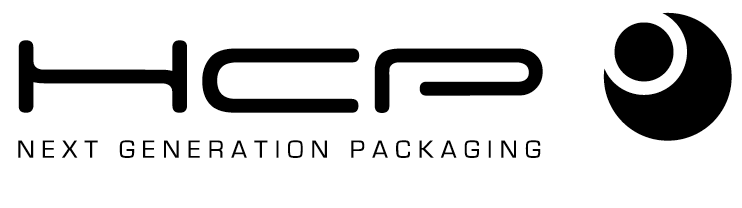