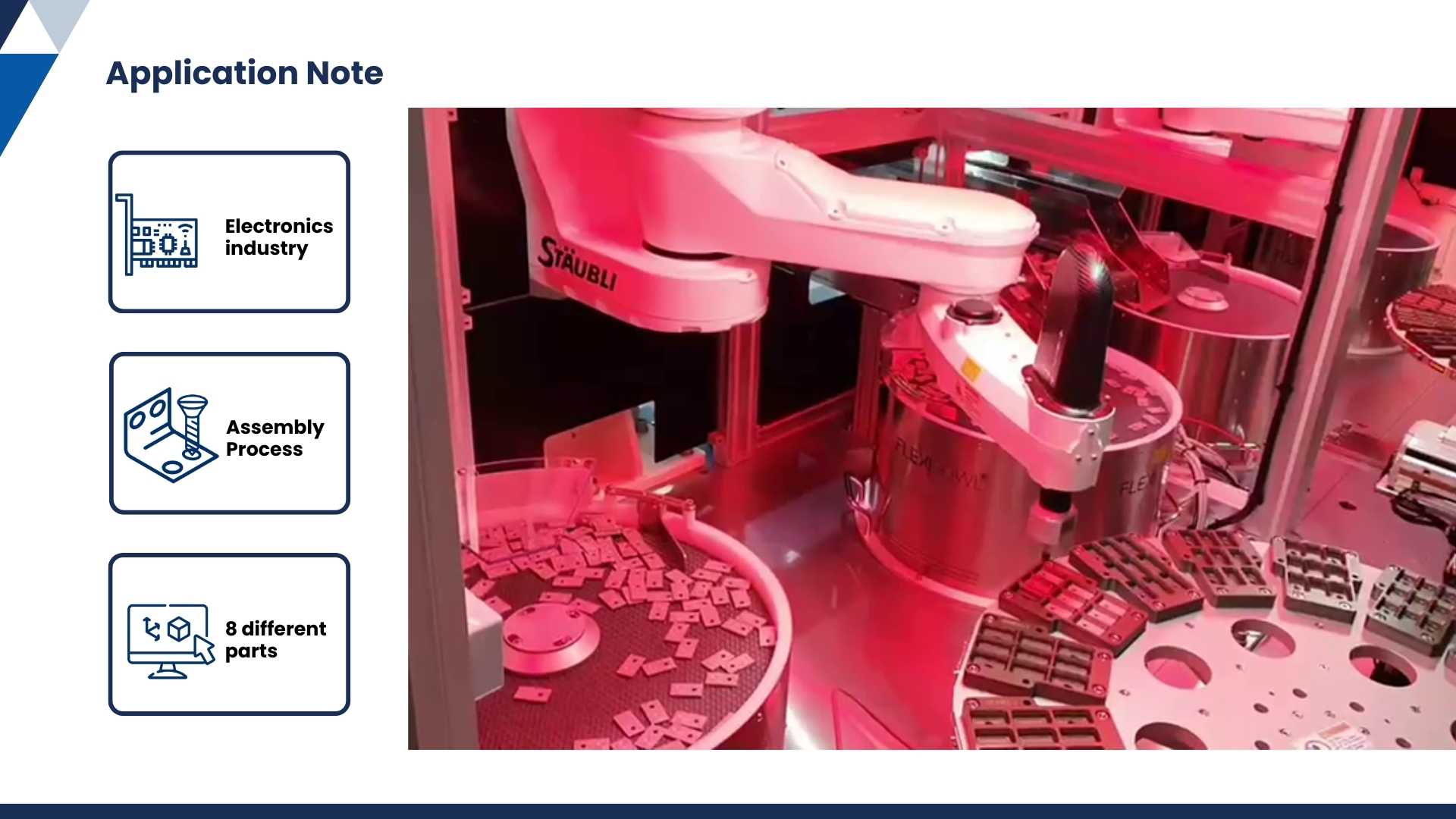
How to feed eight different smartphone battery parts on the same production line, while maintaining high quality and a fast time to market.
Case Study: Flexible Feeding System for Smartphone Battery Assembly
The Challenge
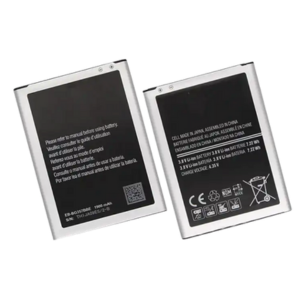
- Handling eight diverse types of components in battery assembly, adapting to various shapes, materials, and sizes for production flexibility and precision.
- Achieving a high feed rate of 240 parts per minute to keep up with the rapid market demands and ensure timely product availability.
- Maintaining a compact layout.
- Upholding stringent quality standards in battery assembly, crucial for consumer electronics.
The Solution
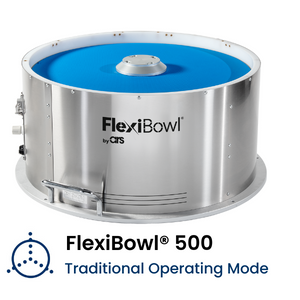
- Integration of eight FlexiBowl® 500 feeders to handle a variety of battery components, providing flexibility and precision in the assembly line.
- Utilization of the FlexiVision vision system for efficient part identification and tracking, ensuring accurate positioning for the assembly process.
- Employment of a six-axis Stäubli robot equipped with a Universal EOAT system, capable of adapting to various product types for enhanced automation capabilities.
- Achievement of a feed rate of 240 parts per minute through the advanced automation line, significantly enhancing efficiency and reducing errors.
The Benefit
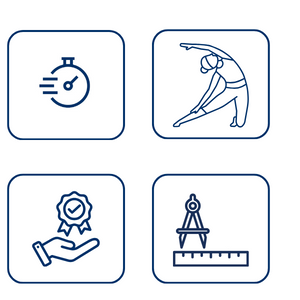
- Performance Boost: Attained a feed rate of 240 parts per minute, enhancing production capacity and efficiency.
- Flexibility and Adaptability: The flexible feeder system handles a variety of parts, with the versatility to adapt to future production line enhancements.
- Quality Enhancement: An automated system that significantly improves product quality through consistent and precise assembly processes.
- Compact and Efficient Layout: Sustained a streamlined and space-efficient layout, optimizing the workflow and facility space utilization.
Abstract
In the face of rapid technological advancements, the electronics manufacturing industry, particularly the assembly of smartphone batteries, faces complex challenges. To address these challenges and meet the demanding standards of customers, an electronics manufacturer has integrated an advanced automated cell into its battery assembly process. This system, with its eight FlexiBowl® 500 feeders, FlexiVision vision system, and Stäubli robot, has significantly enhanced the assembly process, achieving a feed rate of 240 parts per minute and reducing errors. This investment in innovative automation solutions positions the company to effectively address the rapidly evolving demands of the electronics industry.