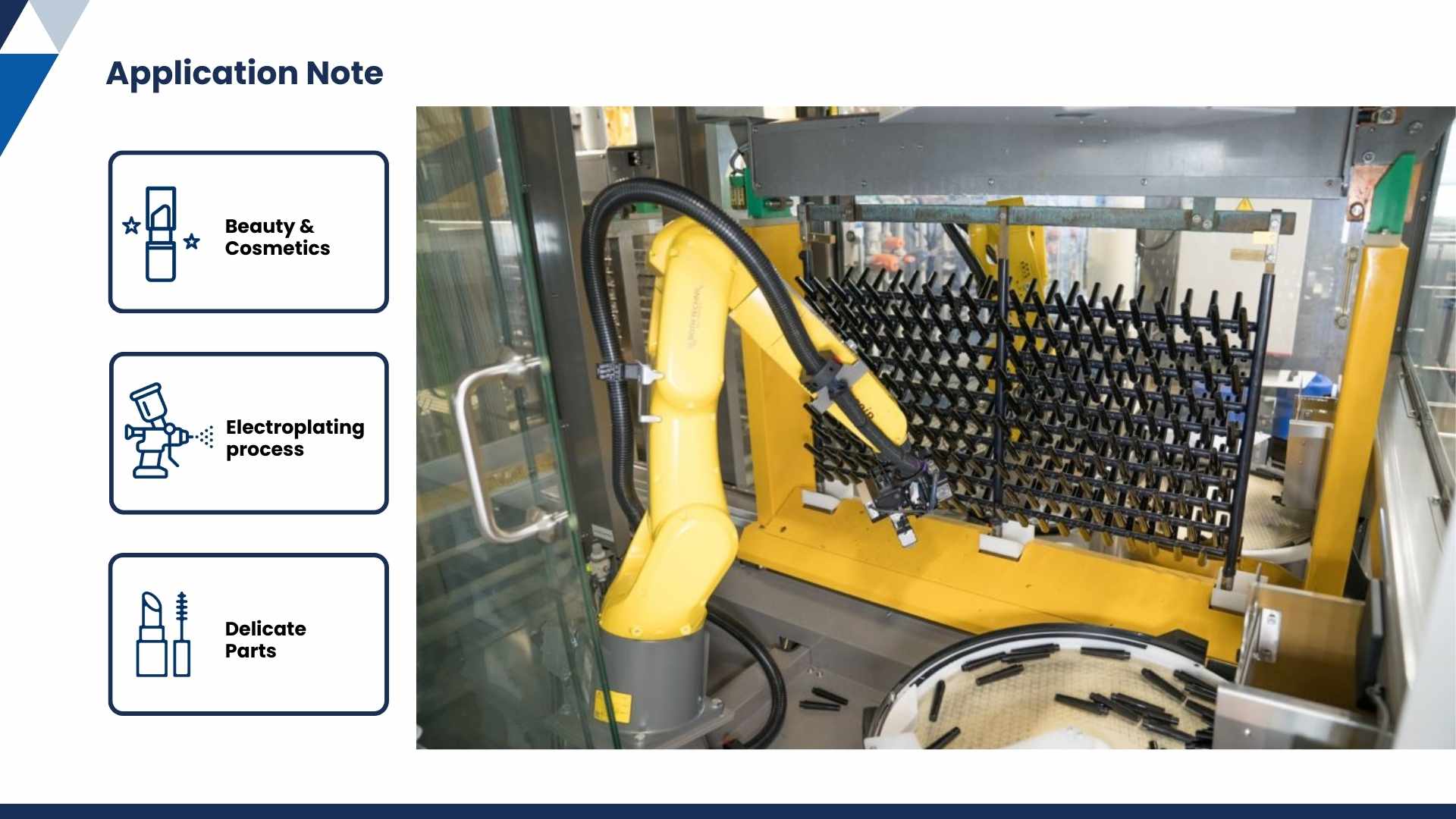
The integration of flexible feeders and smart sensor technology marked a significant advancement in automating the electroplating process, ensuring precision and efficiency.
Case study: using a smart profile sensor from Baumer, four Fanuc Robots Mate 200iD and four FlexiBowl® 650, Roth Technik has developed a fully automatic system for plating racks.
Our partner
Deep passion for design, technology and innovation characterizes Roth Technik. With a broad field of activities ranging from classical as well as emerging collaborative robotics via clever automation solutions, special machine construction, plant engineering and product development, they support you in every phase of your project.
The Challenge
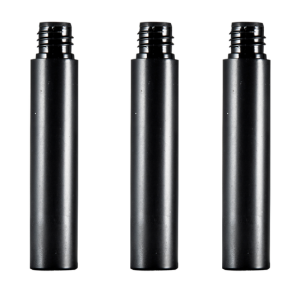
- Automate the electroplating process to address the shortage of skilled personnel.
- Require a space-efficient solution for the handling multiple electroplating racks simultaneously.
- Handle delicate products such as mascara bottles.
- Need to solve the problem of rack position inaccuracy, enabling the robots to learn the exact positions of the hooks for each rack and ensure precise positioning of parts on the electroplating racks.
The Solution
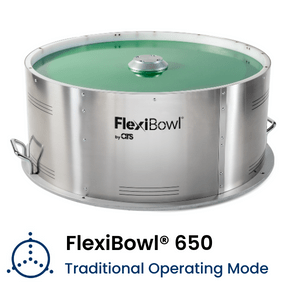
- Implementation of two automated cells, each equipped with two FANUC LR Mate 200iD robots.
- Introduction of two FlexiBowl® 650 per cell. This flexible feeding system can gently separate and orient delicate parts, such as mascara bottles.
- Integration of a compact OXM200 profile sensor by Baumer, mounted on the robot arm, to the exact position of each individual hook.
The Benefit
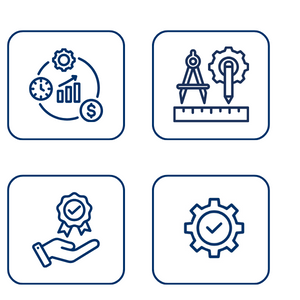
- Automation of the traditionally manual process of loading an electroplating machine, leading to higher profits and ROI.
- Creation of two robotic cells with an optimized layout to maximize space utilization.
- Smooth and continuous parts flow, minimizing bottlenecks and reducing damage to delicate parts.
- Capacity to process 15 million parts per year, increasing production efficiency. Paves the way for future advancements in electroplating technology.
In the specialized field of electroplating, where Collini has implemented its groundbreaking automated system, the demand for innovative, precise, and optimized manufacturing solutions has become increasingly significant. Confronting unique challenges such as the need for high-precision in coating small, intricate items like mascara bottles, the industry is in pursuit of solutions that are not only efficient and adaptable but also sustainable. The integration of flexible feeding technology in this process enhances productivity and accuracy, while also significantly reducing operational costs and times. Crucially, this technology demonstrates its ability to adapt to the specific needs of delicate parts electroplating.
In a strategic partnership with Roth Technik, Collini has incorporated an advanced flexible feeding system into their mascara bottle electroplating line. This setup is complemented by sophisticated robotic technology and a high-precision sensor system, ensuring efficient and precise placement of mascara bottles onto the electroplating racks. The integration of the three-dimensional measurement and detection capabilities of the sensor system is pivotal in this setup, facilitating seamless and orderly processing of the bottles while optimizing space usage.