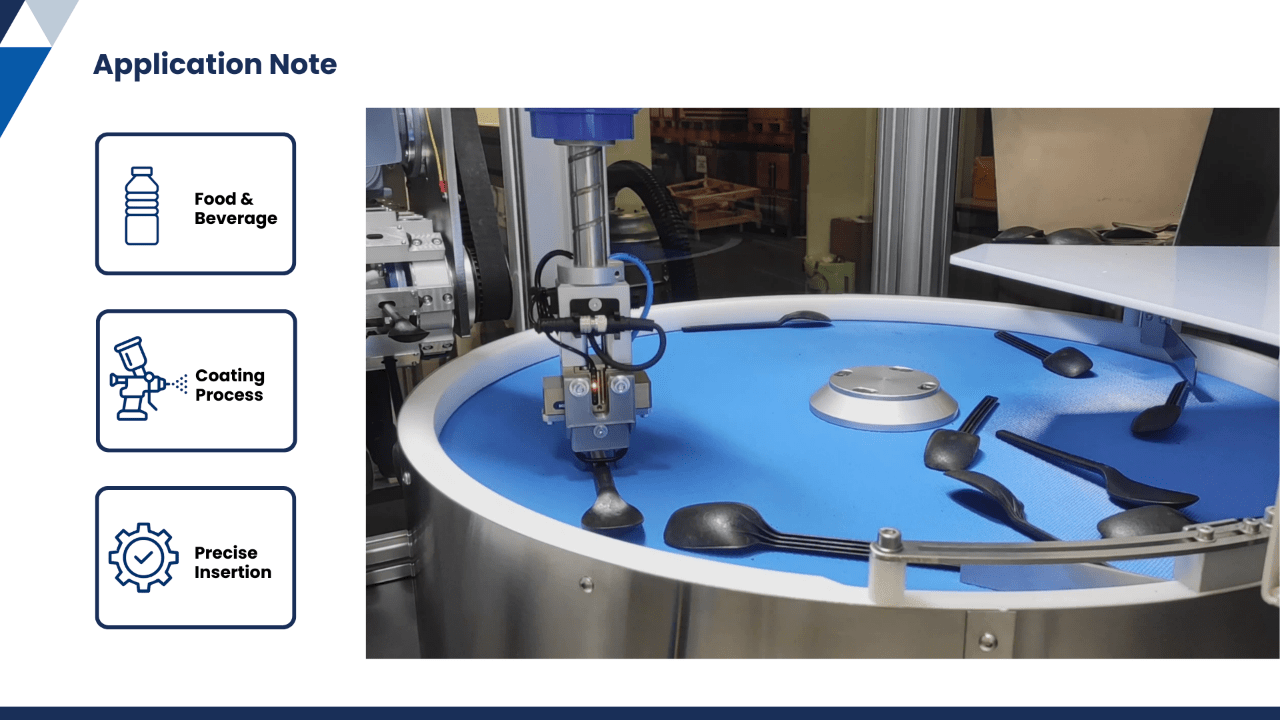
Enhancing sustainable food and beverage production
Case study: a flexible feeding solution applied to a disposable cutlery coating process.
Our partner
For many businesses, making the transition from a manual workstation to a fully automated system can be prohibitively expensive. Another significant challenge is forecasting the demand for future units. Foxbot firmly believes that the future is rooted in smart 2D and 3D camera technology combined with robotics. This approach assures their clients of a rapid return on their automation investments, providing flexibility to adapt to future components.
The Challenge
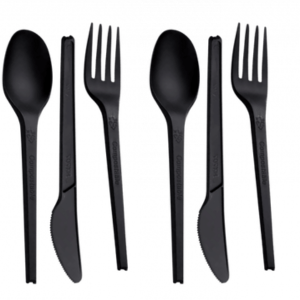
- Handle items of a large size that are prone to overlapping.
- Maintain a compact and efficient layout.
- Minimize waste, increase efficiency, reduce production times and operating costs.
- Many different products to feed.
The Solution
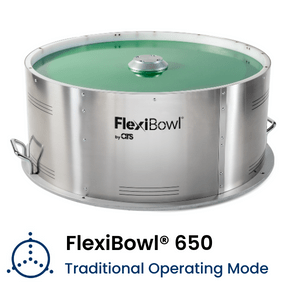
- FlexiBowl® 650 model.
- An Epson robot to pick, orient, and place the spoons in the correct position for the coating process.
- A SCHUNK JGP-P gripper handling the components together with an external re-centering unit for an extremely accurate insertion.
The Benefit
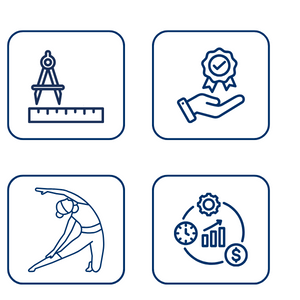
- An optimized layout, that seamlessly handles large, overlapping items.
- Exceptional precision and a significantly increased quality rate for a reliable and efficient production process.
- A flexible feeding solution to quickly adapt to market needs.
- Reduction of machinery investment, leading to better ROI.
“Thanks to the FlexiBowl®, we can do 3 processes at the same time. In addition to dropping new components, we are able to separate and pick them with the robot at the same time. No other system offers these parallel functions.”
Janosch Müller, Member of the Executive Board, Foxbot AG
Abstract
This case study focuses on a project implemented by our partner, Foxbot AG, designed to optimize the production of sustainable and compostable disposable cutlery. Addressing the challenge of handling large-sized items prone to overlap, the project has seamlessly integrated the FlexiBowl® FB 650 model and an Epson Robot into the production line. The result is a flexible and efficient system that minimizes waste, maximizes productivity, reduces production times, and cuts down operating costs. This system ensures precise positioning and reliable performance, adapting to the dynamic needs of the market.
Industry insights
In today's fiercely competitive landscape, sustainability, optimization, and flexibility of production processes are no longer a luxury but a necessity. As we navigate the era of Industry 4.0, there is a persistent need to adapt processes and technologies in response to evolving market needs. An efficient system minimizes waste, maximizes productivity, cuts down production times and operating costs. Flexibility enables rapid modification of the production line to accommodate new products or meet shifting market demands. This is where FlexiBowl® comes into play.