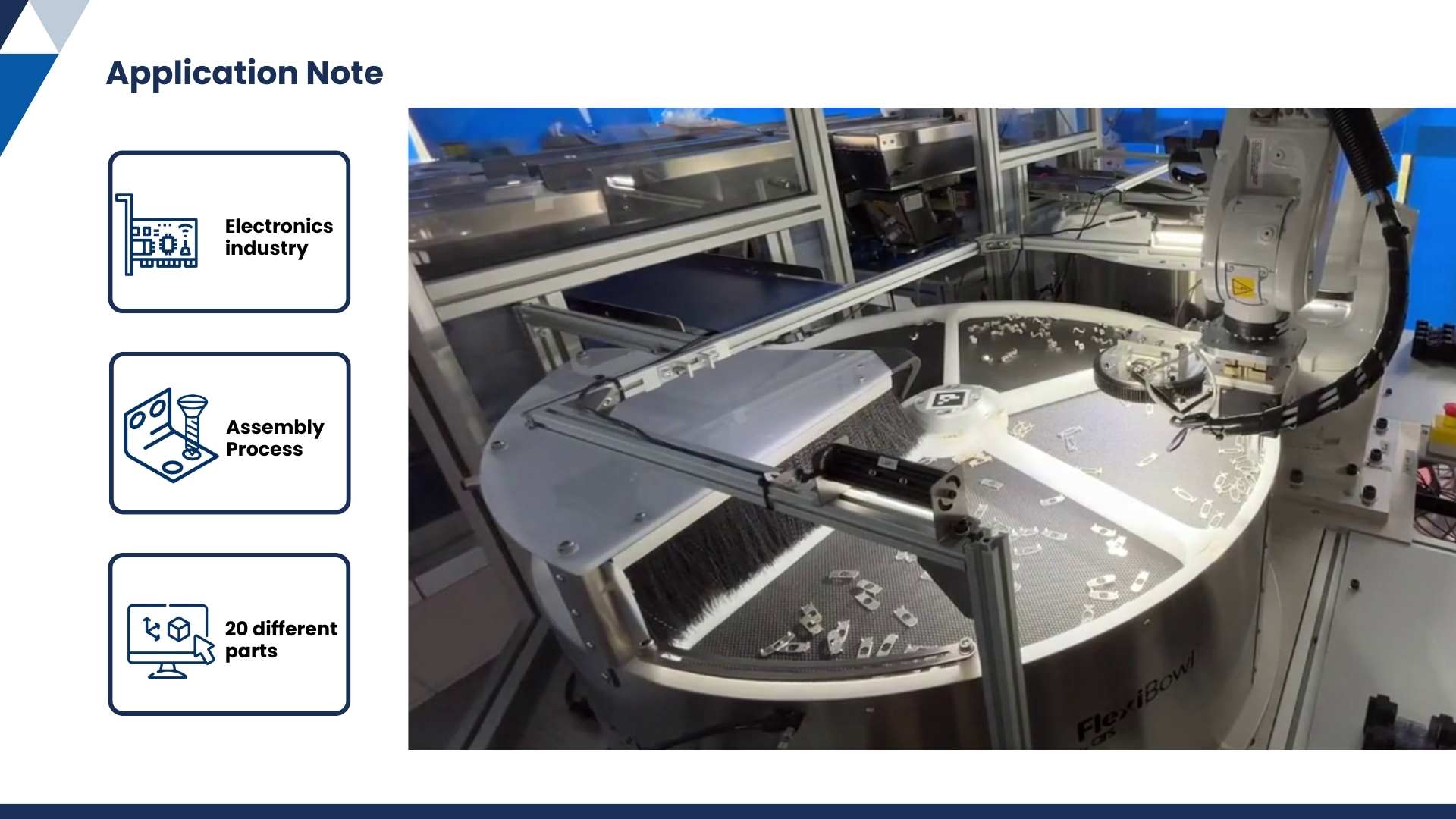
The system handles 20 metal parts in a compact layout, with fast switching between sets of 10.
Case study: a feeding solution to feed ten different metal parts simultaneously.
Our partner
YK-Robotics studies, designs, develops and deploys advanced robotic systems to solve general industry processes needs. The team of talented robotic engineers and machine learning specialists provides a 360-degree service, bringing to your company all the potential of robotics and artificial intelligence.
End Users
Founded as a small company operating in the construction of plastic molds and fine shearing, MSM STAMPI also specializes in molding plastic materials and metals. Over the years the company has developed and strengthened its know-how and now offers a complete and personalized service to meet every need.
ISOLEX activity starts in 1996 producing special insulators made by epoxy resin and microswitches (snap type) specially intended for railway applications. ISOLEX activity starts in 1996 producing special insulators made by epoxy resin and microswitches (snap type) specially intended for railway applications. The skill of the employees in transport industry allows to achieve in a short time a wide range of bearing insulators that thanks to its high quality, are in great demand from the mayor company acting in the electric traction field.
The Challenge
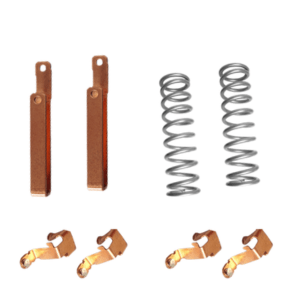
- Manage 10 different metal components simultaneously.
- Be able to adapt change production and manage an additional 10 parts, for a total of 20 different components.
- Maintain a compact layout.
- Minimize waste, increase efficiency, reduce production time and operating costs.
The Solution
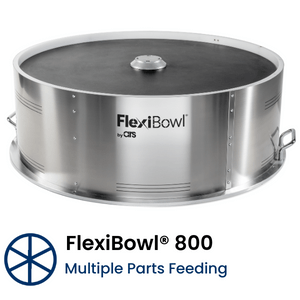
- Two FlexiBowl® 800 feeders equipped with a 5-sector disk, for the simultaneous feeding of ten different metal components.
- An ABB IRB 1200 with an integrated vision system to increase the precision of the process.
- Adopt an innovative hopper arrangement for a controlled and orderly unloading process.
The Benefit
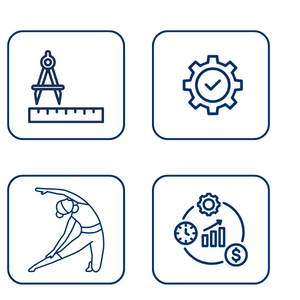
- An optimized production layout with a reduction in machinery investment.
- High precision and a reduced error rate for a reliable and efficient production process.
- Flexibility to adapt quickly to market needs and the introduction of new products.
- The elimination of the need to install customized machines for each type of component, resulting in investment optimization.
“We chose Flexibowl® for this application because it allows us to pick and place different parts in a flexible and compact layout. The ability to handle ten different itmes simultaneously with just two feeders has allowed us to optimize the space within the cell, while maintaining the necessary flexibility for the process”
Simone Sottocasa, Sales & Communication Manager, YK-Robotics
Abstract
In collaboration with our partner YK Robotics, we present a project for improving productivity, which saw the installation of two FlexiBowl® 800 flexible feeders equipped with 5-sector disc to feed metal parts to an ABB IRB 1200 robot. The system allows the management of ten different metal components simultaneously, with the possibility of a quick production change for an additional ten pieces, up to a total of twenty, all in an extremely compact layout.
Industry insights
In the current competitive context, optimization and flexibility of production layouts are essential to stay in the market. We live in the era of Industry 4.0, characterized by constantly evolving processes to meet the changing needs of the market and new technologies. An optimized system allows to reduce waste, maximize efficiency, reduce production times and operating costs. Flexibility, on the other hand, allows the production line to be quickly adapted to introduce new products or respond to market variations.