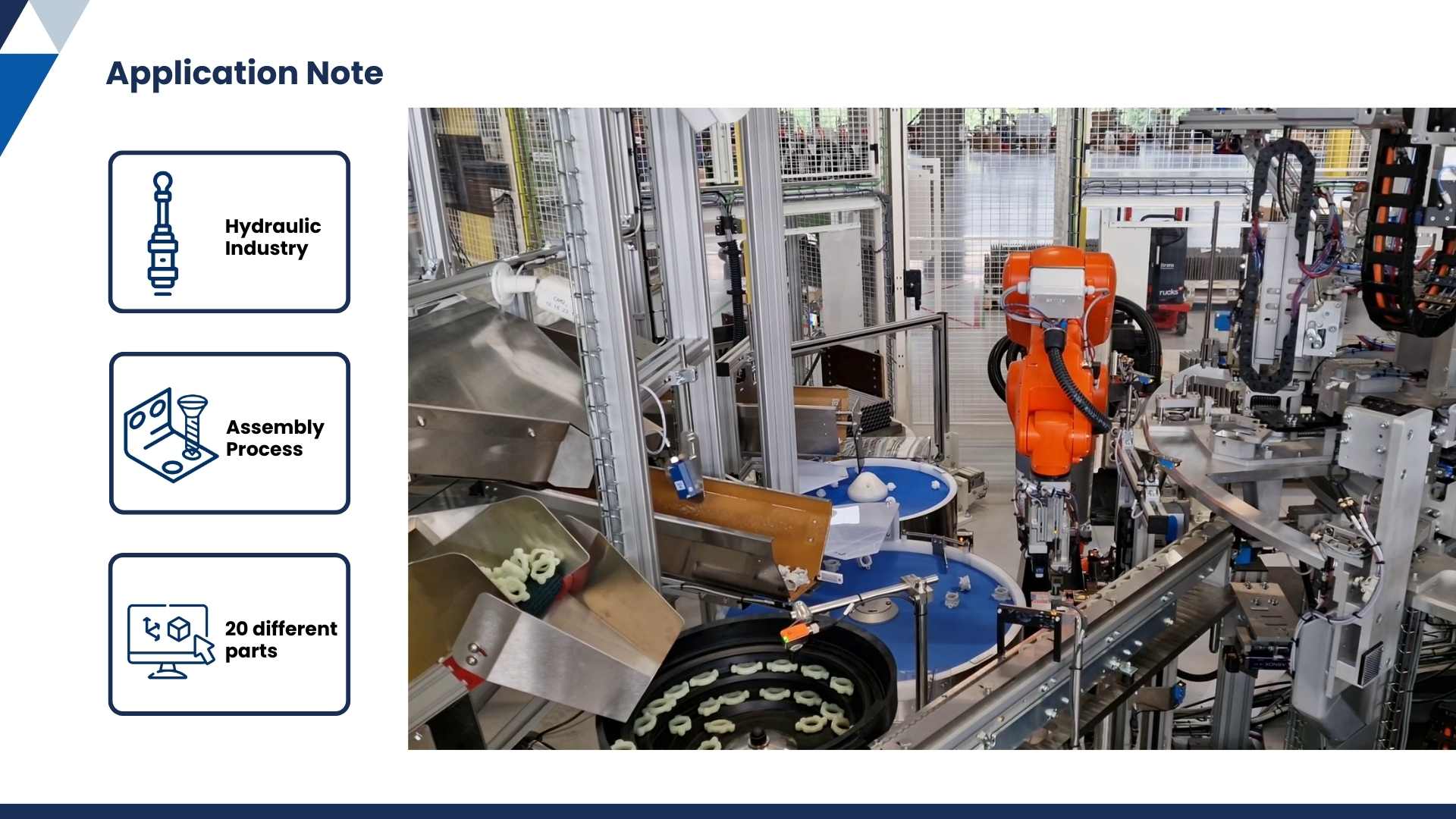
Flexible feeding system for six-component hydraulic assembly
Case study: Six Components, One Line: How to enhance Hydraulic Assembly with Flexible Automation
Our partner
With over 30 years of automation expertise, BILA A/S is a strategic partner for production optimization, helping clients enhance their production processes from simple automation to complete production line upgrades.
BILA A/S brings together all competencies under one roof: consulting, construction, development, implementation, and service. All equipment and specialized tools are developed and assembled in their own workshop, ensuring the highest quality and tailored solutions.
The Challenge
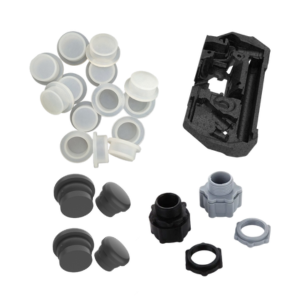
- Maintain high-quality standards in the production of diverse hydraulic components.
- Achieve fast time-to-market for products while adapting to the evolving market demands.
- Implement flexible automation to handle six different plastic hydraulic components on the same production line, facilitating quick changeovers.
- Integrate into existing infrastructure with a compact footprint solution, minimizing space requirements.
The Solution
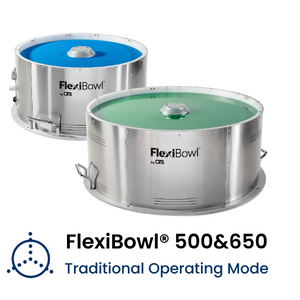
- Integrating an automated cell with two flexible feeders: FlexiBowl® 500 and 650, each supplied by a motorized hopper, to maximize operational autonomy.
- Two KUKA robots are deployed for pick-and-place tasks, enhancing the efficiency of the production line with their precision.
- The quick emptying feature of the FlexiBowl® feeders ensures swift changeovers, minimizing downtime and bolstering productivity.
The Benefit
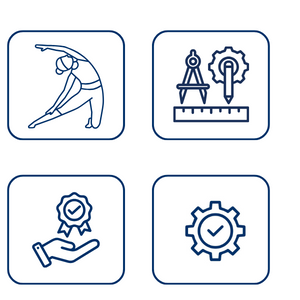
- Flexibility and adaptability: The system's capability to manage six diverse parts demonstrates its adaptability to changing production requirements.
- Compact Layout: The system boasts a compact footprint, ensuring seamless integration into existing infrastructure.
- Elevated quality standards: The precise handling and orientation of components by the flexible feeders ensure consistently high-quality products.
- Swift changeovers and minimized downtime: The quick emptying feature allows for rapid changeovers between different types of plastic components, maximizing productivity and reducing time to market.
“We chose FlexiBowl® because of its high flexibility (one FlexiBowl® handles 3 different parts, another FlexiBowl® handles 6 different parts), its high and consistent capacity, the ability to integrate it into continuous production without buffers at a 10-second cycle time, and the capability to change products automatically in approximately 2 minutes, using one feeding channel and two hoppers.”
Søren Madsen, Project Manager, BILA A/S
Abstract
The manufacturing of hydraulic components is a challenging process due to the high quality and fast time to market requirements. To address these challenges, an automated cell equipped with flexible feeders has been implemented. This system can handle six different plastic hydraulic components on a single production line. The system uses FlexiBowl® feeder models 500 and 650, which are fed by a motorized hopper to ensure maximum operational autonomy. These feeders sort and orient the components, ensuring they are positioned for the next stage. Two KUKA robots pick and place the parts onto the assembly line. The system is compact and can be easily integrated into existing infrastructure.
The adoption of this cell has reduced walk-away time and improved both efficiency and quality. The system is versatile and can handle six different components without the need for manual interventions. This allows operators to focus on higher-value activities. Additionally, the FlexiBowl® feeders' quick emptying feature facilitates swift changeovers between different types of hydraulic components, minimizing downtime and maximizing productivity.