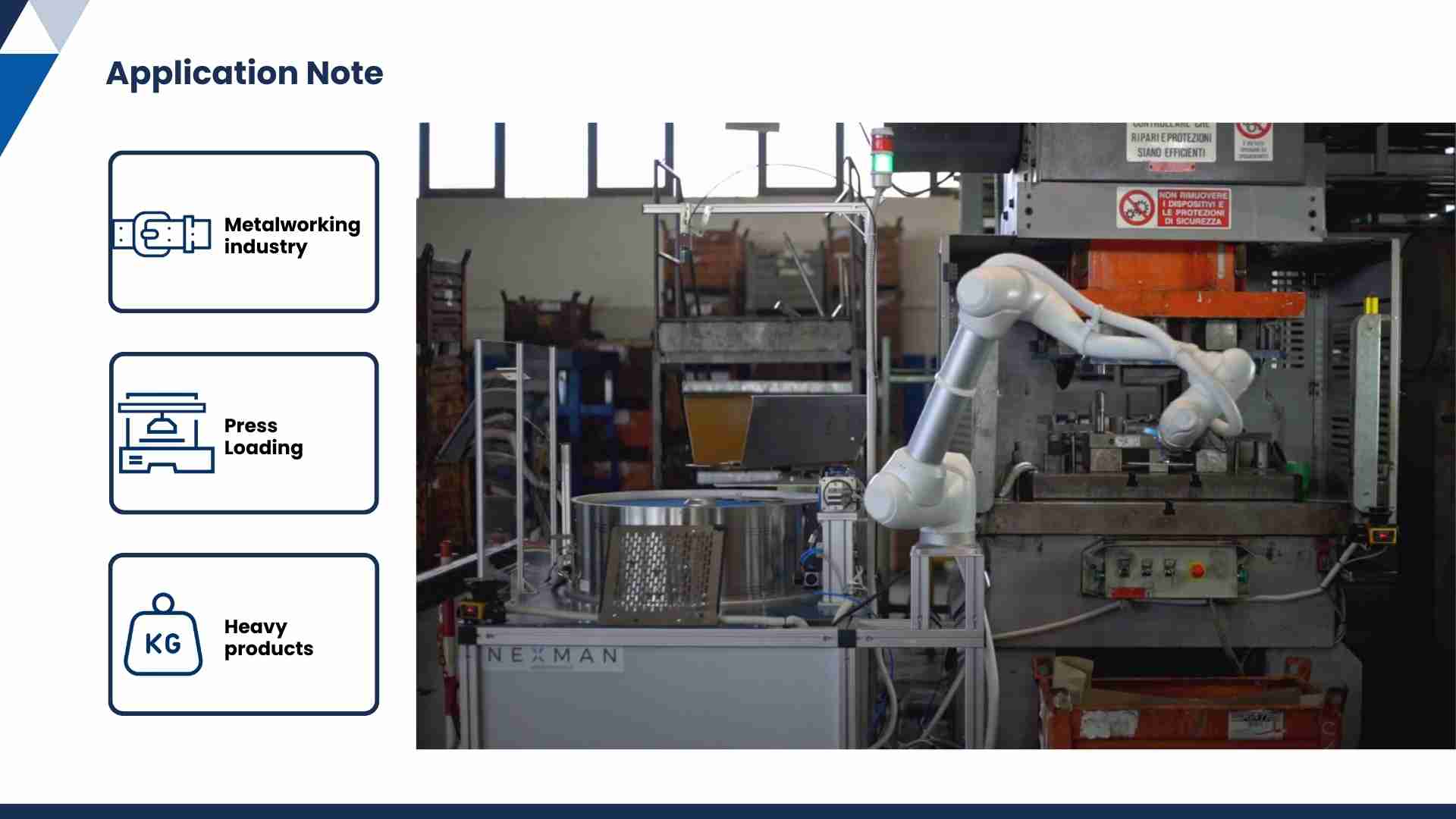
Feeding solution to handle heavy metal parts for a press loading process in the metalworking industry
Case study: a feeding solution to feed ten different metal brackets simultaneously.
Our partner
Nexman assists manufacturing companies in innovating their production processes by introducing robotics, industrial automation, and integrating communication between humans and machines. As a pioneer in the field, they are the first company in Italy to offer industrial automation as-a-service.
The Challenge
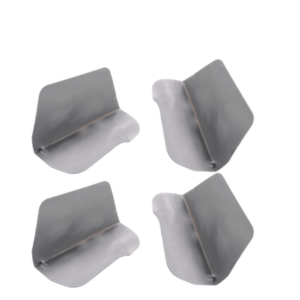
- Implementing an automated pick-and-place mechanism for press loading that not only meets high-quality benchmarks but also encourages a synergistic interaction between humans and machines.
- Efficiently handling a diverse range of metal brackets, which differ in weight, size, and shape.
- Ensuring stringent quality control while minimizing potential mishaps during the handling process.
- Staying agile and responsive in a rapidly evolving global marketplace, all while managing vast volumes of assorted metal components.
The Solution
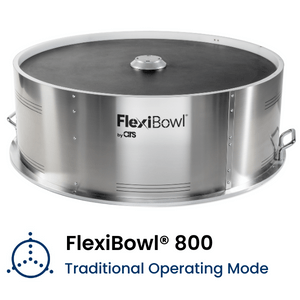
- Collaborating with Nexman to design a system that combines a Doosan cobot with a FlexiBowl® 800 feeder.
- Utilizing the FlexiBowl® 800 feeder to proficiently separate heavy metal brackets, facilitating the cobot's pick-and-place function.
- Directing the cobot to convey each component to a re-gripping station, ensuring meticulous alignment prior to press loading.
- Incorporating a laser safety mechanism to validate the precise positioning of sheets within the press.
The Benefit
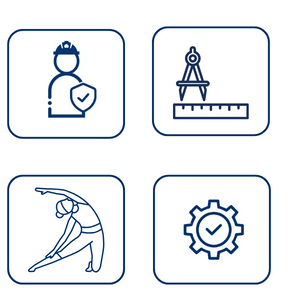
- Fostered a safer work environment through collaborative interaction between operators and the cobot.
- Achieved a compact layout with reduced storage space.
- Integrated a feeder adept at managing heavy metal brackets, flexible and easily configurable for diverse geometries and shapes.
- Developed a scalable system prepared for future expansions and upgrades, minimizing potential production downtimes, and enhanced operational efficiency, achieving significant reductions in error rates.
“The Donati application required the handling of a wide variety of parts. At NEXMAN, we selected FlexiBowl not only for its attributes of flexibility and reliability but also because of our ongoing collaborative relationship with the company across several projects.”
Asia Ravanelli, Marketing Manager, NEXMAN
Abstract
In the evolving world of metalworking, industries face challenges in managing large volumes of diverse and heavy metal parts, such as metal brackets, while maintaining high quality standards. Donati Srl, a leading Italian producer in the sector, looked to improve their press loading process. In partnership with Nexman, they introduced a system that combines a Doosan cobot and FlexiBowl 800 feeder. This system precisely separates heavy metal sheets for efficient pick-and-place operations. Additionally, a laser safety system ensures accurate positioning within the press. This innovative approach has not only elevated Donati Srl's operational efficiency but also fostered a collaborative human-robot environment, ensuring quality and flexibility in production.