
The flexibility of a system describes its ability to adapt to a wide range of possible environments. Flexibility in manufacturing is the ability to reconfigure manufacturing resources in order to efficiently produce a range of products of acceptable quality.
The concept of flexibility comes from the Japanese philosophy of "lean manufacturing," which for many decades has sought to eliminate waste in the supply chain, thereby maximizing quality and efficiency. The "lean" approach came from the Japanese manufacturing industry and is often associated with Toyota. With flexible manufacturing the focus is as much about the alignment of production with flexible market needs, i.e., mass customization, as it is about cost. Automation in this environment is often characterized by rapid tool change-over, batch control, part sensing and a higher degree of integration.
While the "lean" concept has been applied since at least the 1980s and has long been a goal of many manufacturing organizations, new technologies are now making "lean" manufacturing more easily achievable.
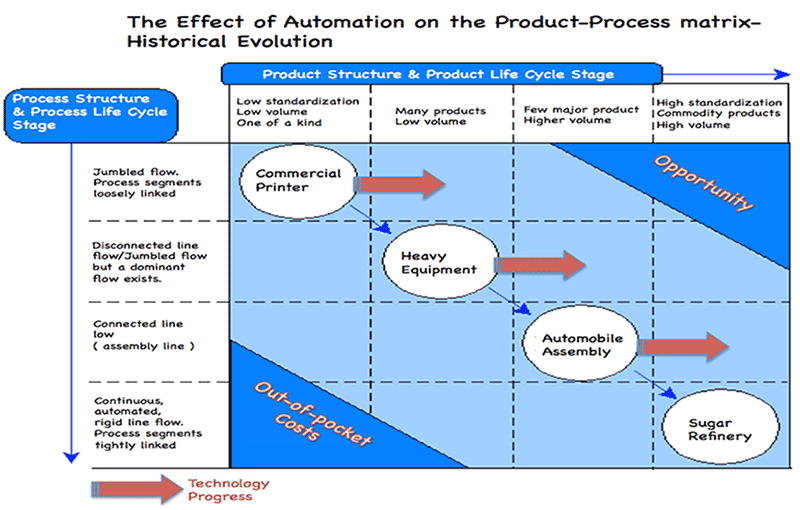
How To Apply a Flexible Assembly System
A flexible assembly system is appropriate when:
- A wide variety of products and/or parts is to be manufactured on the same equipment
- Products have a short life cycle.
- Environmental uncertainties are taken into account in order for a firm to accommodate internal changes and external influences.
- Offshore competition can produce products at much lower costs than can traditional manufacturing methods.
- Parts can be easily damaged by over-handling through manual cells.
- A high degree of accuracy and repeatability is required.
- Parts are too intricate to be assembled efficiently with considerable human intervention.
- Volumes are moderate to high, i.e., cycle time rates are not dependent on the slowest worker.
- Ergonomics is a significant factor.
- The assembly task requires less than roughly 10 seconds.ARS introduced an answer to today's needs called FlexiBowl®, a flexible part feeding system that allows feeding and assembly of entire families of products, thereby minimizing costs and required equipment in the event of product changeovers.
The FlexiBowl® system is made up of a rotating disk that is actuated by a servomotor and an impulse generator oriented perpendicular to the rotating disk.The device allows the proper separation and orientation of parts, so that they can be detected using a video camera and picked up by a robot. The rotating disk can be moved as well as accelerated and decelerated in both directions, according to the geometry and grip between the part and the disk surface.A flexible assembly system that includes FlexiBowl® has relatively little mechanical complexity and can be easily reprogrammed to handle different products. Moreover, the system can be operated by remote desktop control, so that it can be controlled from almost any location that allows an Internet connection. In a matter of minutes, the technical staff can connect to your system and provide any necessary support through the Internet.Flexible assembly systems: Main Features
Our flexible assembly system can produce a wide range or products in small batches and does not entail retooling costs for product changeovers. Changeovers can be made easily in a matter of seconds; our technical staff can provide help if needed.
Up to today there has been a significant number of successful applications in many areas: electrical, electronic, automotive, home appliance, military, medical, cosmetic, fashion accessories, house and personal care, toys and gadgets.
Great results have been achieved even with parts possessing complexities which have typically caused traditional part feeders to fail:- Delicate
- Adhesive surface
- Irregular or cylindrical geometry
- Lubricated
- Tangled
- Presence of burrs
- Silicon and rubber
- Plastic- and metal-molded
- Extremely small
Robotic and visual guidance are integral parts of the flexible assembly system. These can be quickly reprogrammed to reflect changes in production needs and cycles.
The SCARA robot is the most common complement to the system. Some SCARA characteristics such as high reliability, high accuracy and speed, minimum maintenance, ease of use and extremely compact design make this type of robot eminently suitable for working with FlexiBowl®. The system ensures high productivity and, at the same time, high flexibility in assembly lines and production systems. When higher dexterity is required, a 5- or 6-axis arm can also be integrated with the system. A machine video system is then used to locate and ascertain the orientation of the parts.
Flexible Assembly Systems: Benefits
Thanks to quick response and high speed, flexible assembly systems assure:
- Quick and easy setup
- High accuracy and repeatability
- Easy maintenance and cleaning
- Low noise
- Better space utilization
- Compatibility with a wide range of products
- Rapid changeovers
- Circular tracking for a higher cadence
Why Flexible Assembly Systems Are Fundamental
Uncertainty may exist regarding demand, product prices, product mix and availability of resources. Uncertainty may arise from the actions of competitors, changing consumer preferences, technological innovations, new regulations, etc.
Thus, manufacturing flexibility clearly has major implications for a firm's competitive strength and can improve it considerably. This importance of manufacturing flexibility makes it an imperative to include it as a part of the firm's strategy.
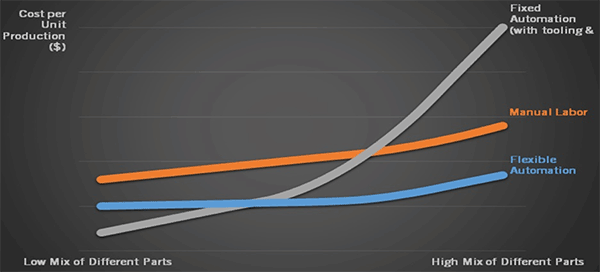