Discover 4 alternatives for Parts Feeding Systems with our infographic. Optimize production with flexibility and efficiency.
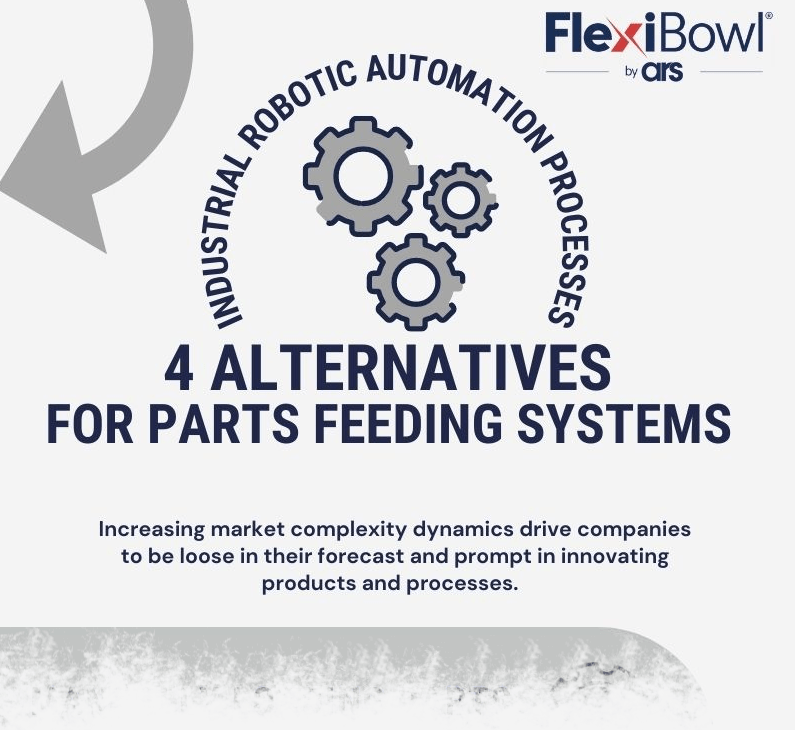
Our infographic reveals 4 alternatives for Parts Feeding Systems, empowering you to optimize production with flexibility and efficiency. The dynamics of increasing market complexity push companies to innovate products and processes for Parts Feeding Systems.
Download the Infographic for Free!
While the traditional manufacturing strategy focused on producing at the lowest cost and highest quality, it's now essential to maximize organizational and manufacturing flexibility and maintain responsiveness in a constantly evolving competitive landscape.
Among various manufacturing processes, assembly consistently stands out as the most costly and complex, largely due to the role of parts feeding.
This article explores four methods to feed parts in an industrial setting, including operator manually loading parts into a system, Vibratory Bowl Feeders, Bin-Picking, and Flexible Feeding Systems.
Operator Manually Loading Part into a System
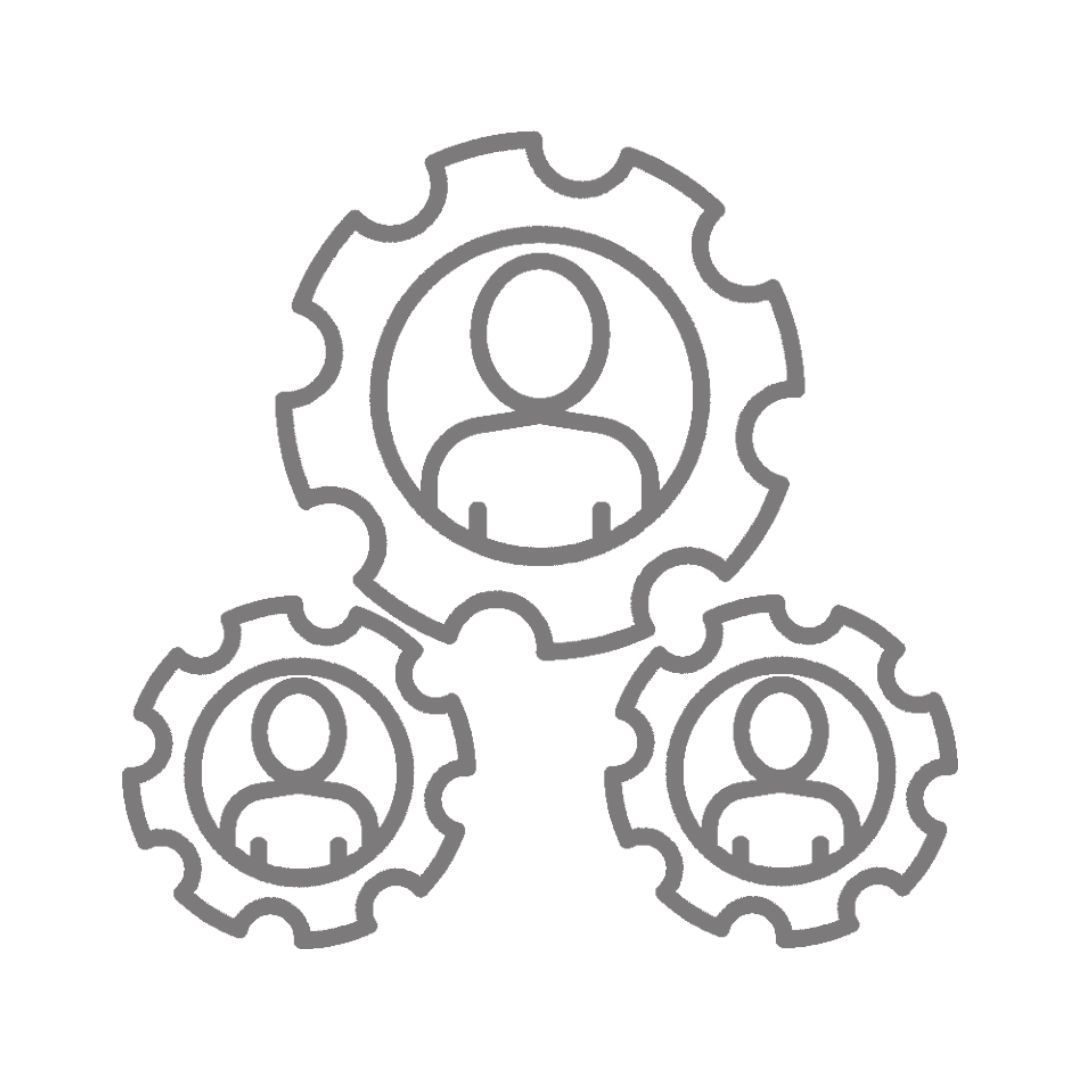
When conventional automation equipment can't handle small batches, or the products are too fragile for bulk feeding, manual organization of products into workpiece trays or racks becomes an option. This method simplifies the assembly process, but the high cost of preparing custom trays or racks makes it unsustainable for managing frequent product innovations.
Alternatively, when dealing with small, varied batches, many adopt parts kitting, another manual assembly method. While kitting can reduce the manufacturing footprint and simplify material handling, it demands substantial manual labor for organizing the kits and handling the parts.
Vibratory Bowl Feeders
One of the most common alternatives among flexible feeding systems is the vibratory bowl feeders.
These systems automatically feed parts, but they are customized for a single product and rely on the product's shape and mechanical behavior. As a result, the manufacturing team must have as many bowl feeders as the number of product types to be made. This can be time-consuming and expensive to change over, and the systems can be noisy and and develop quite a footprint.
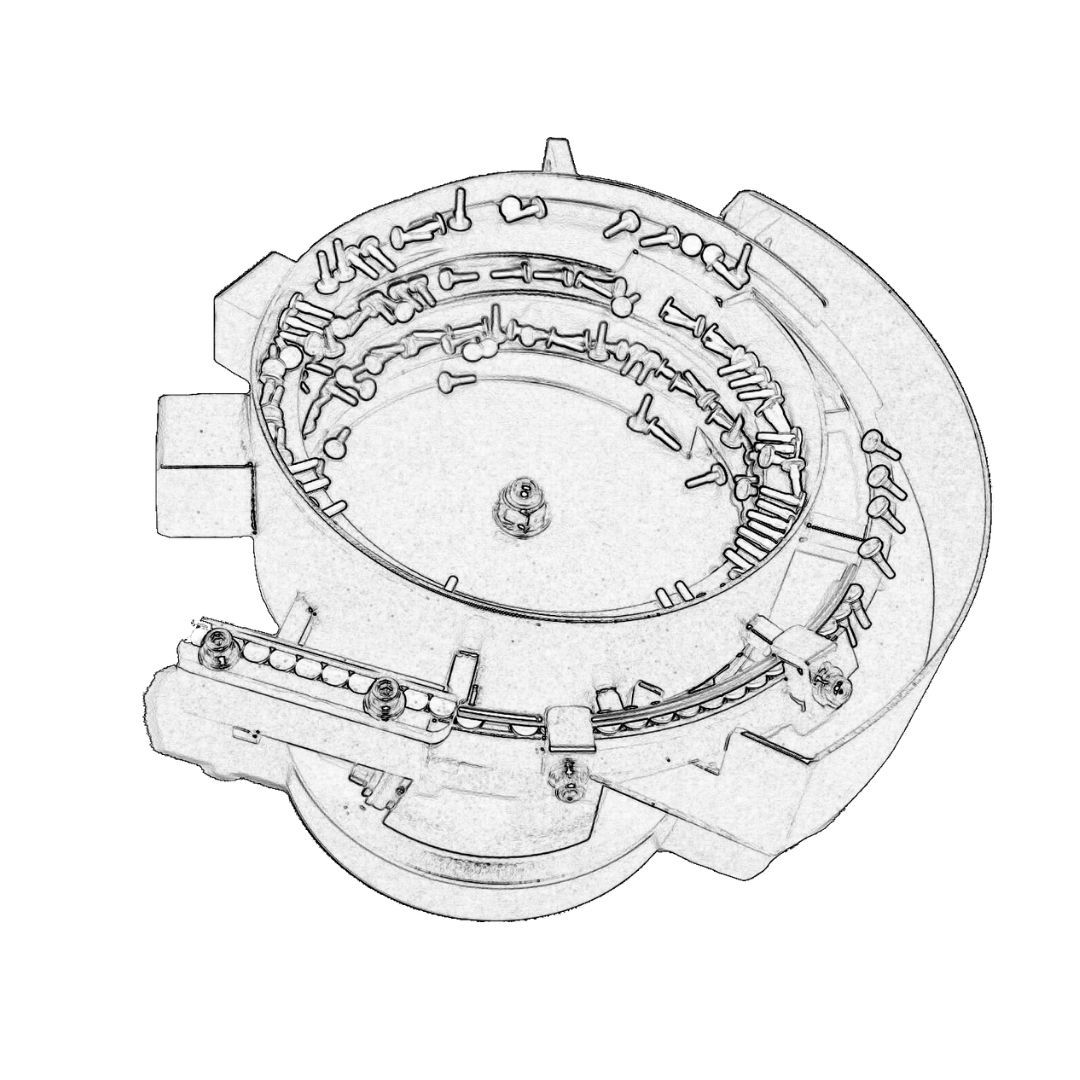
Vibratory bowl feeders are the most common machines used to feed disordered small parts to the production lines, but changing and tuning them also takes time, and discourages performing frequent product changeovers. Sometimes this kind of system can be very noisy, and develop quite a footprint.
Bin Picking
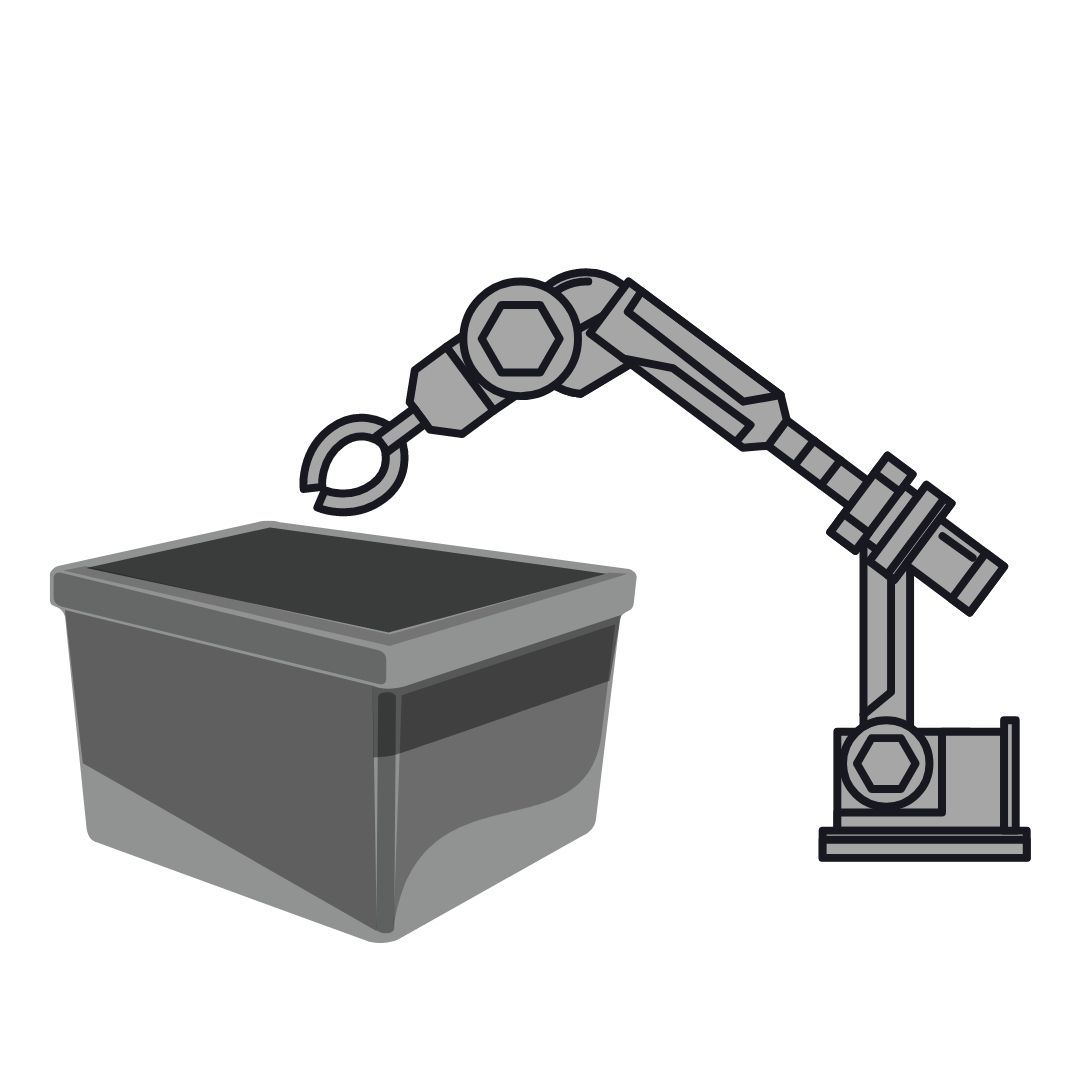
The growing demand for robotic picking solutions has led to the rise of bin picking. It aims to transform traditional manufacturing facilities into smart and robotic production plants that manage small batches as efficiently as mass production. The goal of bin picking is to automatically empty a bin full of bulk products and sort them using a 3D vision system, with either an industrial or a collaborative robot. This solution suits manufacturing processes that store workpieces randomly in metal containers. Though advancements in vision and gripping technologies have improved reliability, there are limitations.
Among these bulk feeding solutions, bin picking work well with larger, geometrically simple, symmetric parts. However, deploying bin picking can be challenging for products with complex features, non-rigid materials, or prone to tangling.
If the products have a lot of different features, present many surfaces in their stable state, are made of non-rigid materials, or are inclined to tangle, then bin-picking will be challenging to deploy.
These systems also require many different pictures to be captured by an operator to match the possible part rest states, and the calculation process may take some time.
Flexible Feeding System
The most versatile solution for picking & placing parts in bulk is using flexible parts feeders. A flex-feeder is a vision-based system that is paired with either a collaborative or an industrial robot to accomplish parts feeding tasks automatically.
With this approach, the products lay on the flat surface of the flexible feeder and 2D vision system detects the parts’ orientation and sends their coordinates to the robot for the picking.
These systems can easily perform a product changeover: sometimes even automatically, if a quick-emptying function is equipped.
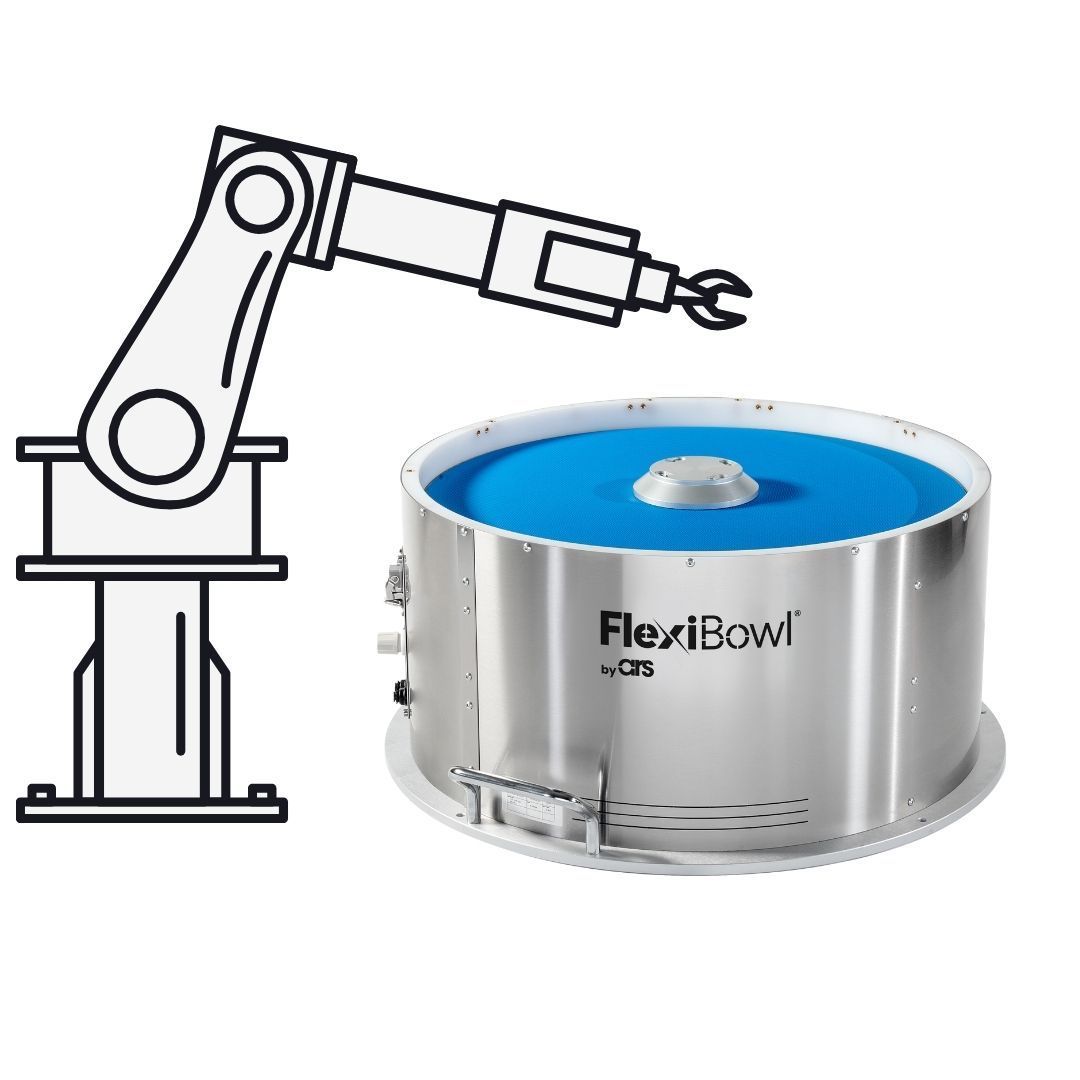
Robotic feeding systems can handle a very wide variety of shapes, sizes, and materials of components on surfaces with different colors, textures, and degrees of adhesion.
For example, sizes ranging from 1 to 250 mm can be handled from a single flexfeeder unit without any issue, in a wide variety of applications, like:
- Tray/belt loading
- Machine tending
- Palletizing
- Screwdriving
- Quality inspection
- Packaging
- Kit preparation
This type of feeder system maximizes its efficiency by making the dropping, separating, and picking processes completely independent and simultaneous.
Some kinds of flexible feeders can handle different types of components at the same time (with surfaces separated in multiple sectors) and work in continuous tracking mode for even better performances.
New Flexibowl® Certified
Robotic flexible part feeding systems markets
The feed rates reached by these systems is so high that they have been employed in several industries, for example:
- Automotive Components assembly systems
- Cosmetics and personal care parts assembly
- Medical components assembly system
- Electronic parts and equipment feeding system
- Metal parts feeding system
- Plastic parts assembly
The continuous possibility of repurposing these systems for new components makes them incredibly cost-effective, as their users can have a single flex feeder for many different parts, and reuse them for a virtually endless series of projects.
Ready to setting your Parts Feeding System?
Drop us a line today for a free quote!