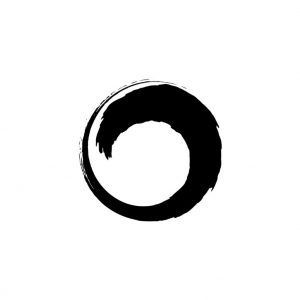
Flexible feeders are vision-based technologies for factory automation that provide manufacturing plants with the possibility to adjust production volumes and spread batches in different machines with minimum set up time.
The flexible feeder is a component of a larger system which includes a robot, a vision system and a bulk feeder.
Parts are stored within the bulk feeder that gradually drops them onto the flexible feeder surface.
The vision system controls the flow of the parts from the bulk feeder to the flexible feeder and sends their coordinates to the robot for pick and place.
There are two categories of flexible feeders in the market:
1. Linear system
2. Circular system
In the linear system, the parts that are released from the bulk feeder fall onto a motor-driven plate which spreads the parts all over.
In the circular system, the combination of a bi-directional rotation and the flipping impulse from beneath, lets the parts separate for the robot pick up.
• Dropping refers to the action of the bulk feeder
• Separating refers to the action of the flexible feeder
• Picking refers to the action of the robot
LINEAR SYSTEM
In linear feeders, parts are released on a square/rectangular plate or belt that is driven by mechanical cams or electric motors. In these systems dropping, separating and picking are sequentially.
Even in the most sophisticated systems where separating is very fast and effective, the resulting cycle time is substantially affected from picking being sequential to dropping and separating. From dropping to picking there is a gap of 2-3 seconds.
CIRCULAR SYSTEM
In circular systems, the disc is split into four functional sectors:
• Dropping
• Separating
• Picking
• Recirculating
By splitting and confining every single phase of the process in a dedicated sector, dropping, separating and picking parallel.
This process usually lasts 0,5 seconds, which is 4/6 times shorter than the former; afterwards the vision system can detect parts and send coordinates to the robot for picking.
In many applications which combine a single circular system with a fast robot the resulting performance exceeds 75 ppm.
The circular system is easily controlled by a set of sw parameters:
– Clockwise and Counterclockwise
– Acceleration and Deceleration
– Speed and Angle
– Number of Flipping Impulses
The proper set of parameters allows the parts to be effectively separated and oriented.
The circular system is compatible with continuous movement and circular tracking, the outputs of a single feeder and robot can even exceed 90 ppm.
The FlexiBowl® falls into the category of circular system.
A striking feature of FlexiBowl® is the high payload, with parts total weight exceeding 7 kg.
Special and customized discs make FlexiBowl® suitable for handling cylindrical, complex and flat-shape parts with size ranging from 1 to 300 mm. Silicon and rubber components are easily fed.
The FlexiBowl® can be used in both harsh (ex.: machine tending, injection moulding, etc.) and clean environments (cosmetics, medical disposables, electronics, etc.).