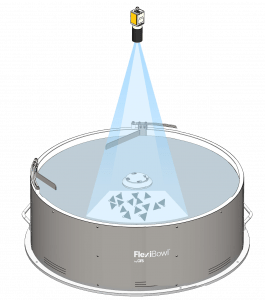
FlexiVision and FlexiBowl: Powerhouses for Vision-Guided Robots
In the fast-paced evolution of industrial automation, vision-guided robots take center stage. Using robots or cobots amplifies precision and boosts efficiency.
Advanced vision systems and robotic technologies are transforming manufacturing processes across diverse industries. Spearheading this change are FlexiVision and FlexiBowl engineered by Ars Automation.
FlexiVision: The Ultimate Vision Software
FlexiVision, the fully integrated video software for robot guidance engineered by Ars Automation, works together with FlexiBowl to optimize precision component handling in industrial automation.
FlexiBowl, as a smart device for flexible parts feeding, has significantly enhanced robotic automation. Complemented by FlexiVision, this dynamic combination enables seamless part feed and handling, ensuring efficient, safe, and effective operations. On this page, you can explore the powerful features of FlexiVision.
FlexiVision: PC-Based Vision Software
for Vision-Guided Robots
FlexiVision stands out as a premium PC-based vision software for robot guidance. It can optionally integrate with FlexiBowl feeding systems. Thanks to its compatibility with the Cognex library, FlexiVision can work with a broad range of industrial robots. Its aim is to simplify the implementation of flexible feeding cells. The system offers a variety of tasks including:
- Dynamic control of all FlexiBowl functionalities such as acceleration, speed, flip, and move forward/backward commands
- Camera calibration
- Template definition
- Object acquisition
- Robotic piece picking
- Place sequences
Cognex Vision Library:
The Key Infrastructure for FlexiVision
FlexiVision leverages the powerful Cognex vision library. It allows easy handling of randomly oriented parts. Parts can be swiftly dumped on the feeder surface, separated, recognized, and picked up by the robot with absolute precision. FlexiVision foresees the inclusion of customized sequences to integrate inspection functionalities on the application. It also offers a simplified programming environment to ensure easy and successful integration of FlexiBowl systems.
Maintained and developed by ARS automation, FlexiVision is the driving force behind vision-guided robots and parts feeders.
The Cognex Vision Library: Comprehensive Communication and Image Acquisition
The Cognex Vision Library provides robust vision software on any industrial camera or frame grabber. Cognex's acquisition technology supports all types of image capture including analog, digital, color, monochrome images, area scan, line scan, high resolution, multi-channel, and multiplexed images. It is compatible with hundreds of industrial cameras and video formats, addressing the full spectrum of acquisition requirements typically used in machine vision.
Cognex Vision Library: Integrated, universal communications and image acquisition for Vision-Guided Robots
With Cognex Vision Library, users get robust vision software on any industrial camera or frame grabber. Cognex acquisition technology supports all types of image capture:
- analog images;
- digital images;
- color images;
- monochrome images;
- area scan,
- line scan,
- high resolution,
- multi-channel,
- multiplexed images;
Cognex supports hundreds of industrial cameras and video formats covering the complete range of acquisition requirements typically used in machine vision.
Machine vision allows an industrial robot to see what it's doing. Without machine vision the robot would be blind – only capable of repeating the same exact task over and over until it's reprogrammed.